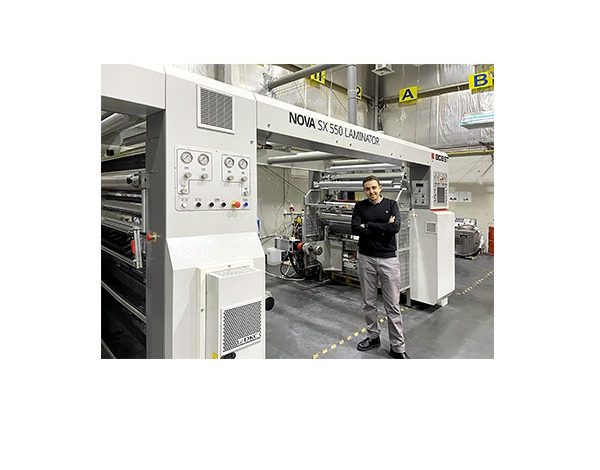
One of the largest label printing companies in the Middle East, Digital Labels has installed the first BOBST NOVA SX 550 solventless laminator in the region to speed up production and offer a sustainable, cost-effective solution to its customers. The machine was put into operation via remote support from Bobst Italia to comply with COVID-19 restrictions.
Amman-based Digital Labels is a specialist in self-adhesive, in-mould, and wraparound labels, and shrink sleeves. First established in 2004, the company has expanded operations significantly over the past few years as it has identified new and profitable market sectors. This includes diversifying into flexible packaging to deliver pouches, flow wrap, liners and bags to customers in the food, drinks and automotive markets in the Middle East and North Africa.
Responding to green demands
Environmental concerns have increased the demand for solventless lamination as customers look to label and packaging producers to introduce more sustainable manufacturing methods for flexible packaging. To meet these requirements, Digital Labels has chosen to invest in the NOVA SX 550 laminator, an innovative new machine introduced by BOBST in early 2020.
“Maximizing sustainability in the process is very important to us,” said Mohammad Sabha, Plant Manager and Executive Engineer. “We launched our own Let’s Go Green campaign back in 2016 to optimise production in the most environmentally friendly way possible, and we are continually looking for ways to improve our green credentials. The NOVA SX 550 solventless laminator fits perfectly with that ethos.”
As a member of the non-profit organisation SEDEX, Digital Labels has also undertaken and passed the extended SMETA 4-pillar audit, which assesses the Environment and Business Ethics of a company in addition to Labor Standards and Health & Safety. The world’s leading social audit certifies that that the company is working in an ethical manner and complying with international standards and good practice.
Agile and cost-effective production
The new modular and compact BOBST NOVA SX 550 laminator offers agile production, with faster set-ups and changeovers to help Digital Labels respond to demands for short runs and quick turnaround with less waste. It handles a wide range of substrates including paper, alu-foil, metallized films and thin stretchable materials, with production speeds reaching up to 450 m/min. Tool-less changeovers of transfer rolls are performed within minutes irrespective of whether solid rolls or sleeves types are used. A complete job changeover is very fast, taking less than 15 minutes.
The flexibility of the laminator enables high-quality production at low cost. Along with an intuitive HMI, it comes with a patented one-touch automated washing system that requires less cleaning solution compared to similar machines and features an adjustable cleaning cycle of five minutes or less.
Automatic reel-centering technology saves on set-up time and waste, and rollers are compatible with other manufacturers’ systems. The unique three-column design, which offers easy access to all parts of the machine, is also contributing to the high uptime, and the data collection and connectivity features allow Digital Labels full control of the process and access to BOBST remote services.
“When I first saw the NOVA SX 550 laminator in the BOBST showroom, I knew that it was exactly what we needed. It is very operator friendly and so easy to use, and it is equipped with all the necessary technologies for fast changeover, like fast fully automatic washing system,” said Mr Sabha.
Remote installation
With tight restrictions on travel and access caused by the ongoing COVID-19 pandemic, Digital Labels’ own team of engineers had to manage the installation themselves, and they did a great job, with a little remote guidance from Bobst Italia.
Due to the true plug-and-play nature of the NOVA SX 550 laminator, which needs no special foundations and is simply lifted into place, the installation was a complete success. Within just two days of delivery, Digital Labels was up and running, producing quality laminated structures for customers – a true testament to the intuitive design and ease of use of this BOBST machine. Mr Sabha commented, “We didn’t have any issues with the new laminator and our products are produced according to the standards.”
Reflecting on the whole process, he said, “We were actually quite surprised by the simplicity of the machine. Although the COVID-19 procedures didn’t allow BOBST technicians to visit Jordan for the installation, our engineering team was able to install it with online support from Italy.” He added, “Our operators are also very satisfied with the machine and learned to run it in a very short time.”
Relying on partnership
A long-term partnership with BOBST has seen Digital Labels install five BOBST flexo presses and a laminator over the years, before this latest acquisition.
Always at the forefront of development, the company was the first printer in the Middle East to implement 7-color Extended Color Gamut (ECG) printing through the investment in a BOBST flexo press with REVO DigiFlexo technology. Other installations include a further three inline flexo presses, a CI flexo press and a compact multi-technology laminator for flexible packaging from BOBST.
“Quite simply, we put our trust in BOBST’s machinery, because we know that we are buying the highest standard, best quality and the latest technology. Added to that, we can also rely on getting the best in after-sales support so that we can minimise downtime and keep our promise to our customers of delivering high-quality solutions on time, every time,” said Mr Sabha.
“We needed to expand our solventless production with a simple machine to handle short runs with short changeover times and the BOBST NOVA SX 550 meets those criteria perfectly. I believe that this machine has a place in every flexible packaging printing house and I’m 100% confident of its productivity. I highly recommend it.”
“With the new NOVA SX 550 solventless laminator in house, Digital Labels is leading the industry by offering sustainable, cost-effective and flexible production to customers looking to improve their green credentials and to meet the end users’ quest for environmentally friendly products,” said Nanni Bertorelli, Product Line Manager Coating & Laminating, Bobst Italia. “AT BOBST, we are committed to working with our partners to implement solutions that continue to improve their processes and help them grow productivity in a sustainable way.”
24 Comments