Understanding Forming, Filling, Sealing, and Lidding Operations
Exploring Sealing, Filling, and Forming Methods and Machinery
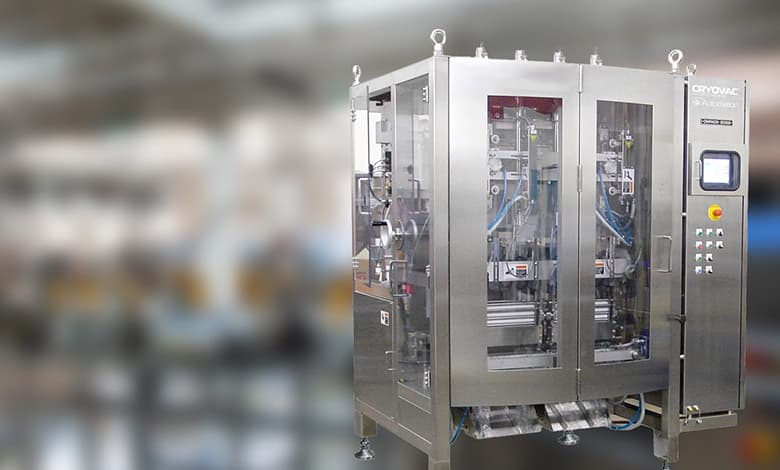
After labels are printed and cut into their final sizes and shapes, they are sent to packaging facilities either in reels or as cut-stack formats to be applied onto bottles, cans, jars, tubs, or other packaged products. Similarly, flexible packaging undergoes a comparable printing and conversion process before being shipped in slit reels or die-cut formats to packaging plants. Here, these materials are used in forming, filling, and sealing operations, flow-wrapped around solid products, or applied as lids or caps for pre-filled containers.
Flexible packaging products, including wrappings, bags, sachets, pouches, and lidding, vary widely in size and purpose. Some packs require vertical filling using single or dual web machines, while others demand horizontal filling or wrapping. Regardless of the method, precise weighing or pre-measuring of the product is critical for efficient packaging. For example, vertically filled packs may rely on precision weighing tables to achieve accurate product weights before sealing.
Sealing methods, such as heat sealing, adhesive sealing, or crimping, depend on the material and application. This variety in requirements necessitates diverse machinery for forming, filling, sealing, wrapping, or lidding operations.
Key Considerations in Packaging Operations
The product’s nature—whether liquid, powder, granules, cream, paste, solid, soft, or hard—influences the design and functionality of packaging machines. Specific equipment components, like hoppers, weighing systems, and transport mechanisms, must align with the product’s properties.
To enhance product shelf life or prevent crushing during transport, some sealing processes include inflating bags or pouches with air or inert gases like nitrogen. Additionally, features such as tear notches, hanging slots, carry handles, reclosable designs, spouts, or perforations can be incorporated into packaging to meet consumer demands.
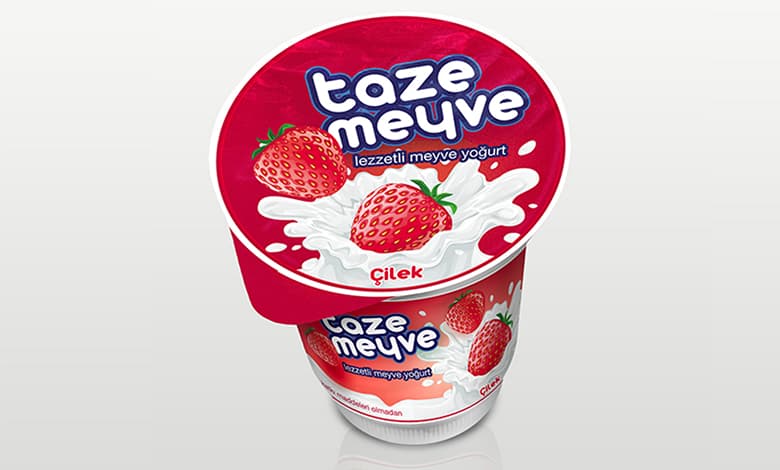
Forming, Filling, and Sealing Machinery
Vertical Form-Fill-Seal (VFFS) Machines
VFFS machines are versatile and compact, requiring less floor space than horizontal systems. These machines are particularly suited for packaging free-flowing materials like powders, oils, and liquids. Key advantages include high-speed operation, reliability, and adaptability to consumer and industrial packaging needs. VFFS machines operate by:
- Forming flexible packaging into desired shapes (e.g., sachets, bags, or pouches).
- Sealing the bottom edge.
- Filling the package with the product.
- Sealing the top, which also forms the bottom of the next package.
Single Web vs. Dual Web Machines
- Single Web Machines: These machines use a single material web to form and seal packages. They create a longitudinal seam using heat or adhesive. Modern advancements, like ultrasonic sealing, enhance sealing through liquids or for heat-sensitive products.
- Dual Web Machines: These use two material rolls to form packages with different materials on each side. They are ideal for applications requiring additional durability or specific material combinations.
VFFS machines are utilized in industries such as food and beverages, pharmaceuticals, and chemicals, packaging products like tea, grains, sauces, or detergents.
Horizontal Form-Fill-Seal (HFFS) Machines
HFFS machines follow a horizontal workflow, requiring more floor space than vertical systems. These systems are often used for stand-up pouches, spouted pouches, and zipper pouches, commonly seen in liquid or snack packaging. Features like nitrogen filling for extended shelf life, spouts, and built-in straws enhance functionality and consumer convenience.
Specialized Packaging Techniques
Flow Wrapping Machines
Flow wrapping machines create airtight, close-fitting packages for confectionery, gift wraps, and butter packs. These horizontally operated machines use pre-printed materials to overwrap products effectively. Key components include infeed conveyors, film forming areas, sealing mechanisms, and cutting heads. The packaging material is formed into a tube, sealed, and cut to individual sizes, offering versatility for food and non-food items.
Lidding Machines
Flexible lidding machines are used for various products, including food, pharmaceuticals, and cosmetics. Common materials include aluminum foil, PET, or paper. Lidding processes often include pre-heating, sealing, and die-cutting to shape. Modified Atmosphere Packaging (MAP) systems can also be integrated to replace air with gas mixtures, extending product shelf life.
Heat sealing remains a key method, with adhesives tailored to the container material. Adjustments in temperature, pressure, and dwell time ensure seal integrity. Lidding films can also incorporate peelable seals, enhancing consumer usability and providing a surface for marketing or informational content.
From VFFS and HFFS machines to flow wrapping and lidding systems, the packaging industry offers a range of technologies to suit diverse products and applications. These systems ensure efficiency, product integrity, and consumer satisfaction, making them essential for modern packaging operations.