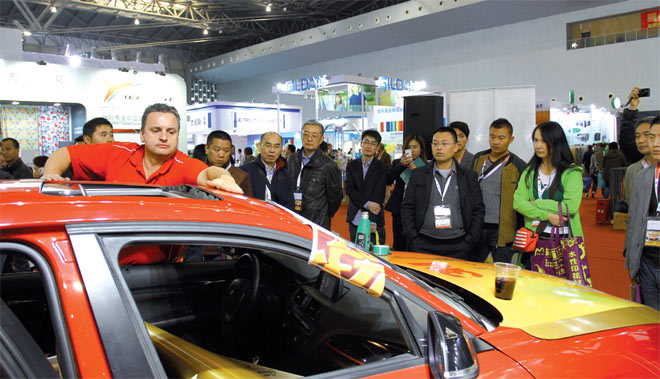
FESPA is returning to China this year, with the re-launch of FESPA China 2019. The new event will take place from 8 – 10 November 2019 at the Canton Fair Complex, Guangzhou, China, where it will be co-located with ISLE Autumn (International Signs & LED Exhibition).
FESPA previously hosted FESPA China events from 2012 to 2015, alternating location between Shanghai and Guangzhou. The last FESPA China event to take place in Guangzhou was in 2014 and attracted 11,667 individual visitors, with total attendance of 15,166 including re-visits. Delegates travelled from 91 countries, both within Asia and further afield.
Roz Guarnori, Exhibitions Director at FESPA, explains: “We’re delighted to be returning to the Chinese market after a four year absence. Speaking with exhibitors at our previous FESPA China shows and other worldwide FESPA events, their feedback shows that there is a strong appetite for a FESPA branded event for the Chinese market. By co-locating with ISLE Autumn, visitors will have the opportunity to attend two leading shows that naturally complement each other’s proposition, delivering added value from their time in Guangzhou.”
FESPA China will occupy hall 1.1 of the Canton Fair Complex, equivalent to 70% of the show floor, with ISLE Autumn taking the remaining 30%. FESPA China exhibitors will be focused on speciality print – screen printing, digital printing, textile printing and printed signage – whereas ISLE Autumn addresses non-printed signage, including LED display and lighting.
Roz continues: “Early demand sparked by initial conversations with exhibitors is coming from both Chinese and international companies, so there will be a variety of exhibitors for visitors to meet and do business with. From our previous experience with FESPA China, we know that visitors are happy to travel to exhibitions in Guangzhou and feel confident that the returning 2019 edition can match the success of our past events. The co-location with ISLE Autumn offers visitors a combination similar to that of FESPA Global Print Expo and European Sign Expo, which has proved appealing for FESPA audiences over the past five years.”
Reflecting the educational content offering of other FESPA exhibitions, FESPA China 2019 will include some free-to-attend show features, details of which will be confirmed in due course.