“Middle East Holds a Special Significance for UFlex Group”
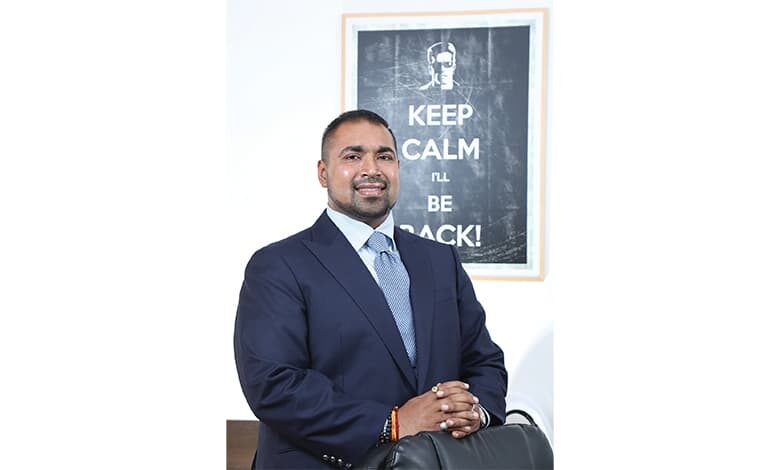
ME Printer talks to Anantshree Chaturvedi, Vice Chairman and CEO, Flex Films International
For the last three-and-a-half decades, UFlex has earned an irreproachable reputation of defining the contours of the packaging industry not only in India, but all around the globe. Founded in 1985, the billion-dollar company has expanded with large manufacturing capacities of packaging films and products, providing end-to-end solutions and serving as a one stop shop flexible packaging solution provider to clients over 150 countries.
Anantshree Chaturvedi, Vice Chairman and CEO, Flex Films International – the global manufacturing arm of UFlex – talks about the future of plastic films, recycling and sustainability, the use of new technology and packaging strategies, trends in the world market, impact of the coronavirus pandemic, and much more.
You are one of the biggest producers of packaging films in the world. However, since there is a global campaign to curb the use of plastic materials, what in your opinion would be the future of plastic films?
UFlex via its global subsidiary Flex Films has been growing aggressively in packaging films space and our latest round of greenfield and brownfield expansion has positioned us as one of largest packaging film producers in the world. We have advanced manufacturing plants in 8 locations globally – UAE, Mexico, India, Egypt, USA, Poland, Russia, and Hungary – with a cumulative production capacity of over 4,65,000 MTA and another two plants coming up in Nigeria shortly and Dharwad (South India). We offer all types of polymer films – BOPP, BOPET, CPP, PCR Grade as well as value added ones like Alox Coated, Metallized and Speciality Films.
The ongoing debate around plastic waste vs realization of importance that plastic holds in our daily life has paved the way for flexible packaging industry to build a sustainable tomorrow. However, this isn’t a new concept for UFlex. Seeing the growth in consumption and hence the rise in packaging, our CMD & Founder Mr. Ashok Chaturvedi had created a parallel recycling infrastructure for mixed plastic waste recycling over three decades back, much ahead of other developed economies. This even won us the coveted Davos Recycling Forum Awards in 1995. We have been working on sustainability led technologies and projects since then to enable green films and green processes, be it our Recycling Machine to homogeneously recycle MLP (multi-layered plastic) into granules (without the need to separate its layers) or our PCR grade films or be it our ‘to be launched’ bio-degradable films.
UFlex has always believed that sustainability will be the driving force that will open both possibilities and opportunities, and will ensure co-existence of plastic and human race in the ecosystem. For this, a collective approach by all stakeholders involved, from production to consumption of plastic would be needed, hence contributing to inclusion of plastic in packaging without worrying about adding to plastic pollution.
- Responsibility of Plastic Packaging Manufacturers & Converters – Plastic manufacturers and converters should focus on inclusion of mono-material, PCR grade and eco-friendly inputs in packaging films that not just reduces the carbon footprint but are easy to recycle. In addition to this, the plastic manufacturers and converters must also comply with the guidelines laid down under the EPR norms to mitigate the problem of plastic waste.
- Accountability of Brands – Brand owners have the responsibility to take back equal amount of post-consumer plastic waste as much as the plastic packaging they sell. They should also focus on methodologies on how to bring back post-consumer plastic waste and also derive innovative ways to prevent plastic deviate from its desired path.
- Consumers – Consumers can trigger more and more need for sustainable packaging with what and how they consume, in turn making the brands adopt green packaging. More importantly, via correct segregation and disposal of post-consumer dry and wet waste, the end consumers can prevent plastic waste from reaching the landfills and ocean beds, which also helps in easy recycling at the recyclers’ end.
- Role of Government – Judicial participation of any federal will play an indispensable role to throw light on importance of existence of plastics. With development of more recycling infrastructure, allowance to recyclers and provision of grants related to plastic, the government of any country can play a more inclusive role to relay the benefits of plastic to masses while keeping a close eye on the problem of rising plastic waste.
There are now a number of watchdog organizations for standardization and monitoring flexible packaging consumption, CEFLEX for example. These institutions also work as advisors to the governments and play a role in legislation regarding the use of materials for packaging. Are you a member of any such organizations?
Organizations that are committed to reduce plastic waste play a fulcrum role to unite the efforts of all stakeholders and create a plastic-waste free environment. To further bolster its efforts to keep plastic in the economy yet out of the environment, UFlex has recently joined Alliance to End Plastic Waste; a Singapore based global non-profit organization with a mission to eliminate plastic waste in the environment.
Through this affiliation as a board member, UFlex aims to contribute to and guide the Alliance and its members about sustainability practices that it has been following for years to mitigate plastic waste issues, thus globalizing these practices and also to learn and implement universally accepted practices.
UFlex will follow the 4Rs approach to tackle the challenge of reducing stock and flow of plastic waste in the environment, i.e. – Reduce plastic at source in packaging structures and using films made from PCR; Recycle via upcycling and downcycling of PET bottles and MLP; Reuse as source substitution via Pyrolysis; Return to the planet in the form of biomass, if the plastic waste remains uncollected.
You recently announced patented BOPET high barrier film F-UHB-M, designed to replace aluminum foil in flexible packaging applications. Apparently, since this product is recyclable as well, will we see more environmentally friendly products from UFlex in future?
At UFlex, we not only work on developing new technologies but also focus on constantly evolving our existing product portfolio of sustainable and value-added offerings. We already have a whole range of up to 100% PCR grade films and can customize more or less all our films into PCR grade version without making it lose any of its properties. We have started upcycling MLP waste into PCR PE films. Then we have single polymer/ mono-materials that are being used in packaging laminates. In other forms of packaging, we had developed KRAFTIKA – a paper-based tube that uses lesser plastic at source and replaces it with virgin kraft paper; green UV LED inks and water-based adhesives; and much more.
With the launch of F-UHB-M Packaging film, UFlex has been able to successfully replace aluminum foil in a structure with highest levels of barrier and metal adhesion and promote easy recycling. At present we are working on a host of innovative films powered by a sustainable mindset and are most excited about our enzyme based biodegradable technology that makes the uncollected waste turn into biomass.
You have production facilities around the globe, including in the UAE and Egypt. What types of films are produced in these factories and what are their production capacities?
Our manufacturing plant in Dubai houses a BOPET film line with a capacity to produce 22,000 MTA and with our recent brownfield expansion in Dubai (UAE), we will be adding 18,000 MTA of CPP films for our patrons in UAE.
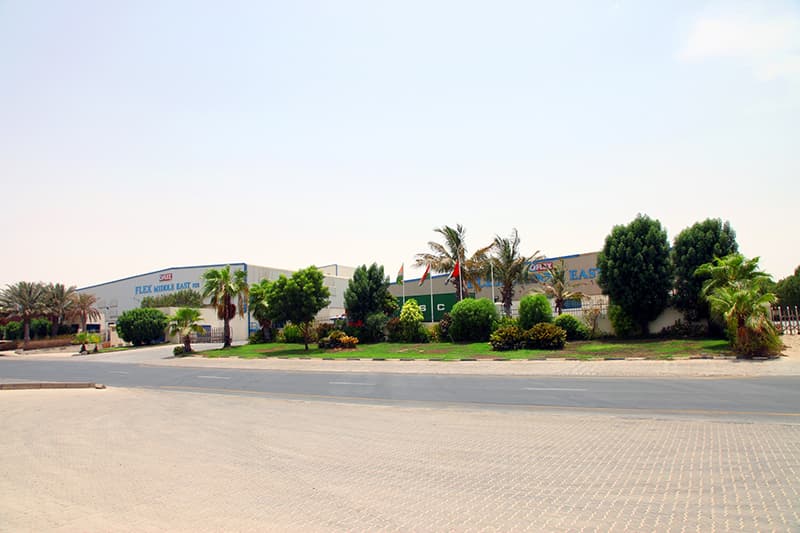
Our Egypt plant at 6th of October City is the only plant in Africa to house BOPET, BOPP and CPP film lines within one facility. We recently made a brownfield expansion there too taking our capacity for BOPP lines to 77,000 MTA; BOPET line capacity stands at 30,000 MTA and CPP line at 7,000 MTA. Besides, our Egypt plant also offers value added and specialty films through advanced Metallizers and Alox Coaters installed at the facility.
How important is the Middle East market for you and do you see it as a growth market?
Being the first location where the group expanded overseas and as the mother of all our global packaging film plants, Flex Films Middle East holds a special significance for UFlex Group and ever since has been a key location for us. Flex Films Middle East operates from the renowned Jebel Ali Free Zone which is the flagship free zone of DP World business hub. This facility of FME holds a 6.7 m wide BOPET line with a production capacity of 22,000 MTA and a 2.5 m wide plasma enhanced high-barrier metallizer with a capacity of 5,400 MTA to manufacture value added and specialty products. This line caters to the packaging requirements locally as well as exports into Middle East regions. Being a preferred packaging partner for the local clientele, FME with guidance from the headquarters located in India is dedicated to meet the demands of both brands and converters in the Middle East region and has evolved exceptionally well for us over the last 15 years of our existence there.
Middle East Market has accomplished the common goal of trade reforms and has contributed significantly towards higher productivity per capita income growth. With efficient logistics network, this zone acts a chain link as well as gateway for distribution. Going further, we are hopeful of the packaging sector to witness growth at a CAGR of 6% which is higher than world’s growth. Having said that, it is also an extremely competitive market making it a “survival of the fittest” situation. UFlex being a reputed name in the industry has backing of some long-lasting relationships built on strong foundation of credibility, world class service and quality delivered consistently. This also helps us in leveraging the best of this market.
Despite the pandemic your Q1 results was impressive. How did you manage to mitigate the efforts of the coronavirus crisis?
The pandemic saw unusual patterns across the world and lowered the pace of global economy, where many businesses were left with no option but to come to a standstill. Unlike many other sectors that were drastically impacted, packaging industry, at large did not face the issue of de-growth. Rather there was a direct demand creation for packaging and packaging materials for essential commodities due to hoarding of food and pharma stocks across the masses, resulting in surge in demand from Jan 2020 till September 2020 and subsequently it normalized.
UFlex being a major supplier of packaging for FMCG and Pharmaceuticals sector is categorized as an essential manufacturer. Our teams worked swiftly to procure all the necessary authorizations in place from the local administration, across the various locations, to continue our manufacturing operations in the tough times. Despite the bottlenecks on transport and logistics front in the initial phase, UFlex traversed past all challenges and laid emphasis on meeting the surge in requirements of packaging and packaging material, especially for certain category of products in food and personal hygiene space that took a sharp surge in first wave phase. With our strong global network, we continued our operations and supplies to our business partners, convertors and CPGs, even in the most difficult to operate scenario.
But not even once did we compromise on the safety and well-being of our people who worked beyond the call of duty in the harshest times. We ensured all protocols of proper sanitization of places and equipment, social distancing, staggered shifts, counselling etc. needed to make them feel cared for.
Not only did we meet the escalated demand for packaging, but also ensured that our expansion plans of commissioning new lines in locations such as Russia, Hungary, Poland and Egypt were not disrupted and we managed to have the lines running in almost the estimated time. These new lines helped us meet the demand as well as add to our overall turnover.
Did the pandemic make you rethink your plan for future developments?
The pandemic outbreak was unanticipated and had made many global organizations halt or defer their expansion plans. Though in the initial phase there were some hiccups due to the uncertainties but we did not let the pandemic derail our global expansion plans and were able to continue it, as projected. Even during the pandemic outbreak, we were successful to make greenfield and brownfield expansion at various strategic locations across the globe in a view to step closer to our customer base.
Our business growth largely rests on our global approach as we have a firm belief that localization is the key. In the last fiscal we were able to commission our BOPET film manufacturing line in Russia and Poland with manufacturing capacity of 30,000 MTA and 45,000 MTA respectively; and BOPP film manufacturing line of 42,000 MTA. In the last quarter, we have stepped closer to our customer base near Hungary with our new facility that holds a BOPP film manufacturing strength of 42,000 MTA. Our Nigeria plant with a BOPET line is ready to be commissioned anytime soon.
Seeing the encouraging demand for packaging materials, we have even announced an ambitious project in India where we are setting up a new plant for packaging films after a gap of 16 years. This new facility will come up in Dharwad in South India and shall house a BOPET and CPP film manufacturing line with a cumulative capacity of 63,000 MTA. Our Dubai plant will also undergo a brownfield expansion with a new CPP line being put up, as mentioned earlier. We announced doubling of capacity of our Aseptic liquid packaging plant which will commence production of 7 billion aseptic packs per annum in the short run.
We didn’t let the pandemic stall our plans for sustainability projects either and have announced new recycling infrastructure in Mexico and Poland to upcycle post-consumer PET bottles waste into up to 100% PCR PET film Ascelpius and another PCPR line to recycle post-consumer multi-layer mixed plastic waste to make molded, injection molded and extrusion molded components.
What types of packaging films are more in demand now and why?
The pandemic outbreak imparted a lot of lessons to the world and none of us is in a position to face another calamity. Over the past few years, the tug of war between use and ban of plastics in packaging has unearthed avenues of sustainability and eco-friendly materials for packaging manufacturers. Not just packaging manufacturers, converters and brands but even the consumers at large are cognizant about the environment and prefer to pick those packs that serve dual purpose of keeping the food safe and fresh for a long time and does not leave a negative impact on the environment. This sentiment towards environment preservation and restoration has triggered the use of recycle ready, sustainable and value-added films that meets the interest of all stakeholders with reduced carbon footprint.
The tilt of demand is definitely more towards mono-material films that enables material simplification for better recycling efficiencies; advanced barrier films that also supports material reduction like replacement of aluminum foil (as seen in our new F-UHB-M film) and PCR grade films. Asclepius is the range of PCR grade films from the house of UFlex, is quite popular amongst convertors working with environmentally responsible brands.
Based on your experience, what type of packaging is more popular in the Middle East countries?
Smart, sophisticated, minimalistic with MAP (Modified Atmosphere Packaging) feature packaging is more common in the Middle East market. With the escalating debate on plastic waste pollution, we are expecting to see greater demand of sustainable and environmentally friendly packaging in the coming years.
Biscuits, pasta and spaghetti, confectionery, ketchup, molasses, personal care products, frozen food, juices etc. are the primary market segments deriving packaging demand in the MEA region.
You are also offering prepress materials and consumables for packaging industries, including cylinders, flexo plates, flexo sleeves, and chemicals. What is the share of these products in your overall turnover?
Our Cylinder and Inks & Adhesive business together contributes to roughly 16-19% of our overall group turnover.
Could you explain about your research and development activities? What is the process to test a product before its launch into the market?
Over the years UFlex’s focus on its Research & Development activities has not just coined products of excellence for the humankind but has also played an instrumental role in writing success stories for the organization.
At UFlex, we lead our developments of new product keeping in mind the factors of sustainability, product excellence rendered by best properties, business environment and economies of scale. As a plastic manufacturer we are cognizant of the fact that the virtues of plastic cannot be replaced by any other product, and sustainability is the key to a better future, hence our R&D works to develop products that are sustainable and do not harm the environment. Our up to 100% PCR content-based film Asclepius is a testament of our concentrated focus on sustainability quotient. We have also developed a biodegradable film that will decompose the pack into biomass if left uncollected, trials of which are underway.
One of reasons that drive us to develop new products is to deliver beyond what the competitors offer in the market. The team also works towards defying its own standards by offering improved quality of products and also conducts extensive research on polyester and BOPP to create brand new products by developing special resin and specialty films. Its commitment to launch quality products that makes a mark of quality innovation and is used by customers with trust, makes UFlex’ product portfolio speak for itself. For us, innovation of a new product is driven also by what is needed by the customers as on date or by what could witness demand in future.
There is a strict process we follow after an opportunity to conceptualize a product that suits customer’s requirement is analyzed. After thorough deliberations and research, a film is prepared either by development of resin and film through reverse engineering or through off line coating route or core research on new polymer resin and film, aligned with customer requirement. The new products are tested in lab for validation to ensure desired quality is achieved without any deviation. Once the product is developed, it is sent to the trial unit where standardization of quality is re-ensured via sampling.
After internal validations, the developed product is sent to three external parties (customers or testing agencies) for further validation and approvals. The R&D team takes into account feedback of all the parties and the product is said to be developed only if it is approved by all the parties. It is only after approval from all, that the development is sent to the marketing team for commercialization.
90 Comments