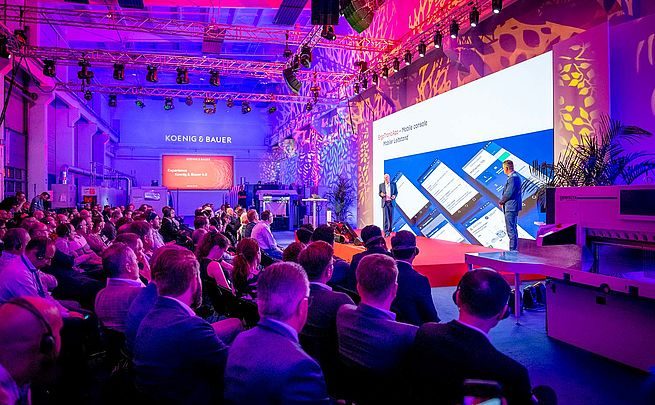
On 20th and 21st May, Koenig & Bauer invited print professionals from all over the world to an open house spotlighting the potential for digital transformation and data-driven services in packaging printing under the motto “Koenig & Bauer 4.0 – Packaging Printing & Connected Services”.
The open house picked up the thread of a customer event held under the same name last year. For the first time, it was now possible to show the complete process chain for packaging production in a live demonstration – from creation of the jobs in the MIS, via printing and die-cutting through to completion of the folding cartons. Koenig & Bauer has thus positioned itself as a one-stop partner for all the needs of this growth market.
As participants in a panel discussion, Stefan Segger (Koenig & Bauer Digital & Webfed), Dr. Peter Lechner (Koenig & Bauer Flexotecnica), Franc Freixes (Koenig & Bauer Iberica), Markus Müller (Koenig & Bauer Coding) and Pinar Kucukaras (Koenig & Bauer Duran) provided key information on their current technology solutions for packaging printing.
The visitors were subsequently able to follow the definition of pharmaceuticals packaging jobs in Optimus Dash. In addition to the basic job data, this involved also specification of the substrates and coatings, the required quantities of different product versions, the corresponding die-cutting formes and much more besides. All process steps through to incorporation into the production schedule were shown live. One key benefit of Optimus Dash is a packaging module with which production jobs, including die-cutting, can be created automatically. The result is a fully imposed PDF.
A six-colour Rapida 105 PRO with inline coater was on hand for the print production. After plate changing, inking of the rollers and automatic register correction, the press produced several print jobs fully autonomously in an AutoRun process. In other words, it switched automatically between production and makeready upon completion of each job in the defined sequence. The operator simply selected the job list, which was then processed as a whole without any further intervention.
Dirk Winkler, head of print technology at Koenig & Bauer Sheetfed, used the time freed up by the autonomous process to explain the underlying quality control concept and to present the Rapida LiveApps. The ErgoTronicApp can be viewed as a mobile console which provides access to the full scope of press functions. The operator can call up all relevant information from the press on a mobile device, for example job data, production times, press status messages and maintenance reminders, including help texts describing the tasks to be completed. With the ProductionApp, on the other hand, it is possible to manage store room inventories and track consumables batches. Even retrospectively, the app provides a precise overview of which print jobs were produced with which batches of substrates, inks and other consumables.
After printing, the sheets were passed directly to the Ipress 106 K PRO for die-cutting, creasing and stripping. Folding and gluing, finally, was handled by an Omega Allpro 110. The visitors were thus able to convince themselves that the promise of high speeds also applies to post-press processes, and were for the first time able to take home a finished folding carton.
Two breakout sessions were devoted to new solutions for the printing and finishing of both high-volume and luxury packaging. Alongside, experts from Koenig & Bauer and Optimus offered detailed information on MIS solutions for the applications concerned.
For the high volume session, production was assigned to a brand new Rapida 145 whose extensive feature list included a high-speed package for printing outputs up to 18,000 sheets/hr, AutoRun, DriveTronic SPC, SFC, SRW and VariDry dryer systems of the latest generation. It produced three typical but very different food and non-food packaging jobs at maximum speed – in an autonomous process and with non-stop pile changes. Low-migration inks were used.
A seven-colour Rapida 106 coater press then repeated production of the packaging from the morning demonstration, though now using Extended Gamut Printing with seven colours in an Esko Equinox workflow. It was thus possible to make a direct comparison between the folding cartons produced with standard and spot colours. The quality and colour reproduction were found to be identical.
Visitors who chose to attend the luxury packaging session were again able to witness a complete process chain: A six-colour Rapida 106 in a double-coating configuration printed one job with opaque white, LED-UV inks, UV coating and a micro-embossing effect applied through the second coating tower, and a second with UV adhesive, cold foil application, LED-UV inks and high-gloss UV coating. These jobs were subsequently embossed, creased, cut, scored and stripped on the rotary die-cutter Rapida RDC 106. The individual blanks, finally, were separated on a Laserck Master Blanker.
The print professionals who came to Radebeul returned home after exciting days packed with a wealth of new information, and must now decide which processes and know-how they will be implementing in their own companies. Certain, however, is that they will soon be experiencing many of the new automation and service tools introduced during the open house in their regular communication with Koenig & Bauer.