Mastering Label Design
An In-Depth Guide to the Pre-Press Process
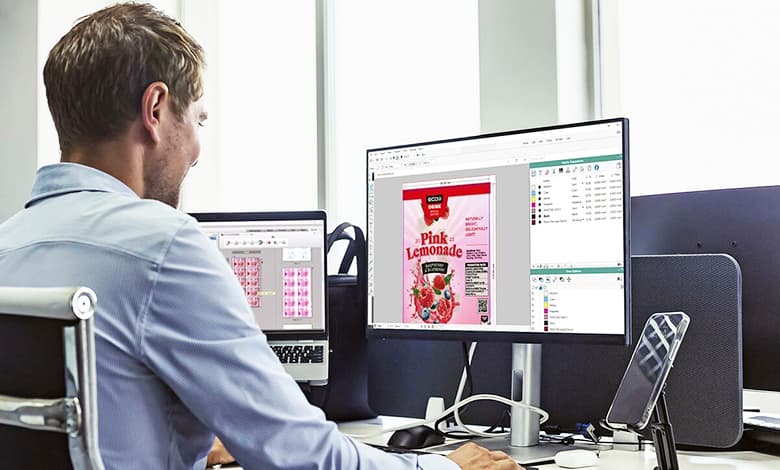
An in-depth understanding of the design-to-print workflow is essential for ensuring that every print job meets quality expectations. This guide offers a comprehensive look at the sequence of steps involved in transforming a label or packaging design from initial concept to final, press-ready format. Familiarity with these processes and the related terminology allows designers, production teams, and stakeholders to anticipate potential issues and address inconsistencies throughout the production chain, resulting in higher-quality outcomes.
Evolution of Pre-Press and Repro Processes
“Pre-press” encompasses all preparations needed to make labels and packaging ready for printing. It includes multiple stages, each requiring precision to maintain consistency, color accuracy, and design integrity. Key pre-press components are illustrated in Figure 1.1 and include:
- Design and Origination: This foundational stage involves creating and finalizing the label or pack design, including typography, layout, and imagery. Artwork must be finalized to ensure high resolution and proper formatting for the selected print medium.
- Preparation for Printing: This stage is critical for optimizing the artwork for production, encompassing color correction, image sharpening, resizing, and ensuring that all elements align with production specifications. The repro process aligns the design with the physical constraints of printing, ensuring colors, textures, and details remain consistent.
- Proofing: Integral to quality control, proofing occurs at multiple stages to preview designs as they will appear in their printed form. Digital proofs, press proofs, and even 3D mock-ups are employed for client approvals and internal validation. Proofing ensures that any issues with color, placement, or text are resolved before production, saving time and costs associated with reprinting.
- Output: This phase involves creating the materials needed for the actual print run, including film production, plate making, or digital assets for modern printers. Plates, films, or other media are generated based on the specific printing process (offset, flexographic, or digital) to match the requirements for accurate and high-quality reproduction.
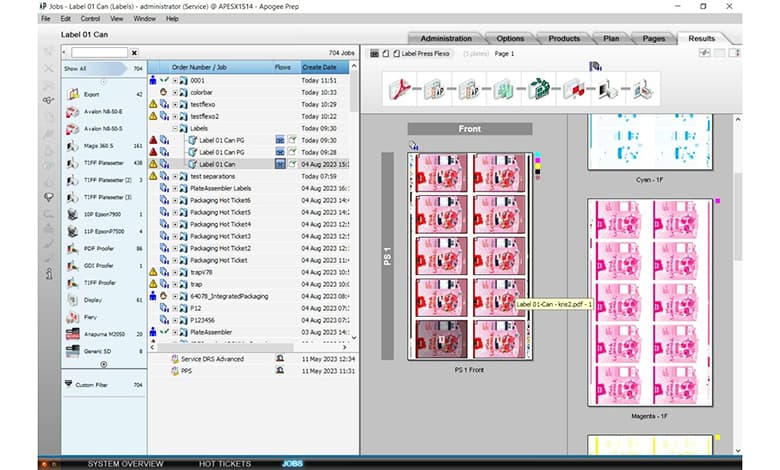
Traditional Pre-Press Activities
Before digital technology, pre-press was an intensive, skilled, and manual process with numerous critical steps:
- Typesetting: Text elements were meticulously arranged by hand, often using movable type or hand-lettering. This process was essential for clarity and layout accuracy.
- Artwork Preparation: Designers and artists created artwork directly on boards, combining text, images, and graphics manually, with minimal error tolerance.
- Proofreading and Copy-Editing: These rigorous tasks ensured that text content was accurate and free from typographical errors. Copy-editing also adjusted text for clarity and coherence, often using annotated symbols.
- Screening and Color Separation: High precision was required to separate colors using the CMYK model, often involving multiple filter applications to ensure each color was isolated correctly. Photography was used to capture each color layer for the large-format print plates, while screening was applied to control the tonal qualities of images.
- Inspection and Retouching: Films and transparencies were reviewed on illuminated tables for imperfections, which were then corrected by hand. Hand-retouching of films and plates was common to maintain image quality.
- Manufacturing of Plates: Creating the physical plates for printing required a high degree of manual skill, precision, and patience.
Transition to Digital Pre-Press
By the mid-1980s, a significant shift occurred with the arrival of computers, particularly the Apple Macintosh and early PCs, along with desktop publishing software like Adobe InDesign and QuarkXpress. Adobe PostScript, a page description language, enabled precise on-screen manipulation of design content and straightforward communication with printers. The result was a shift to computer-aided pre-press, where manual processes were largely replaced by digital methods, increasing efficiency and reducing labor costs.
In the early 2000s, digital processes fully replaced traditional techniques like darkroom development and large-format cameras. The widespread adoption of standardized file formats, including Adobe PDF, revolutionized document sharing and consistency across the industry, providing a reliable format for high-quality, reproducible documents and layouts.
A New Era in Design
Today’s pre-press environment integrates a global, digital workflow that combines computers, the internet, scanners, and high-resolution imaging equipment, enabling designers to work from any location. Modern tools allow for remote adjustments and corrections, with proofing technologies (inkjet, thermal dye sublimation) that deliver near-final quality for review by clients and teams. This allows for easy last-minute modifications to colors or layouts and eliminates the need for costly rescheduling by enabling proofing at remote or client locations.
Rapid job turnaround, flexibility in design adjustments, and layouts optimized for production have become industry standards, reducing costs and increasing efficiency. The adoption of digital printing further accelerates the process, enabling high-quality prints at speeds unmatched by traditional methods.
Overview of the Design Process
Most costs and time in a design project are incurred before production begins. Planning and the creative phases are crucial; errors at these stages can lead to extensive rework or adjustments, which are both costly and time-consuming. Figure 1.2 outlines the typical progression from planning and design to production, with pre-press activities carefully planned to meet the print specifications.
The Need for Pre-Press Expertise
An essential aspect of pre-press is anticipating the effects of the specific printing process and preparing the design data to meet customer expectations. Pre-press specialists must understand, quantify, and document the client’s specifications to ensure accuracy. This stage, explored in detail in this guide, is pivotal in translating creative design into physical print while managing client expectations.
Summary of the Design-to-Print Workflow
Figure 1.3 on the following page presents an expanded view of the 35 critical steps involved in the design-to-print process. Each phase, from initial design to final proofing and printing, must be handled with precision to avoid costly errors. A thorough understanding of each step is essential to ensure a smooth transition from design to production, with the selected printing process influencing specific pre-press procedures.