BOBST Opens New Competence Center in Italy
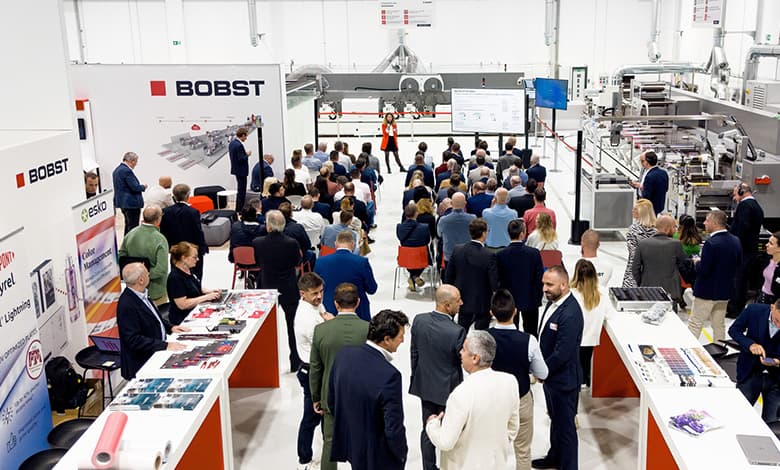
Expands demonstration capabilities and global footprint in labels and flexible packaging production with state-of-the-art facility in Florence
With over 350 employees dedicated to narrow mid web printing and converting, BOBST continues to advance its vision for the future of labels and flexible packaging production, centred on connectivity, digitalisation, automation, and sustainability.
With a growing installed base of over 1,300 narrow mid web presses, the company has expanded its demonstration capabilities and global footprint in this segment with a new state-of-the-art competence center in Florence, Italy.
Following the successful establishment of the Atlanta competence center in the US, BOBST has opened a brand-new 1,200 sq m competence center dedicated to labels and flexible packaging, located in Florence. Providing access to the company’s full range of printing solutions with six complete production lines (including inline flexo, digital, and All-in-One technologies), the new Italian BOBST facility is designed to serve customers through proximity and local expertise, as well as being a hub for collaboration and innovation.
Between 8-10 October, the more than 200 customers who attended the grand opening of the new facility in Florence witnessed a complete overview of BOBST’s value proposition for the narrow mid web market, including pre-press, machinery, technology area, the cloud-based digital platform BOBST Connect, and final applications. The event was supported by leading industry partners representing the whole ecosystem across the value chain.
“The major investment in the narrow mid web printing and converting product line demonstrates Bobst Group’s strong commitment to this segment,” says Matteo Cardinotti, Head of Bobst Narrow Mid Web. “BOBST has experienced exceptional growth in labels in recent years and we are supporting that development by opening more local competence centers and hiring more staff worldwide. In Italy specifically, we have also expanded our production facilities and reinforced our service organisation to match the needs of our European customers.”
Connected end-to-end solutions for labels and flexible packaging
As seen at drupa and Labelexpo Americas 2024, the industry is moving beyond innovation in hardware and software in isolation towards full integration of processes. In this respect, BOBST is leading the way with its portfolio of complete workflows designed for the future of packaging production.
At the event in Florence, guests could experience live demonstrations of the entire ‘Label Solutions by BOBST’ portfolio. BOBST’s All-in-One concept, with inkjet and flexo technology inline, was presented by the DIGITAL MASTER 340 modular label press running pressure-sensitive labels for the beauty segment. For inline flexo, BOBST MASTER M5 demonstrated single-pass production of multi-layer labels featuring oneECG (extended color gamut) technology and DigiFlexo automation.
The production lines on show included a complete solution for short to medium-run flexible packaging applications – a BOBST MASTER M6 flexo press perfectly integrated with a near-line mid web laminator, the BOBST NOVALAM MV. This setup, in combination with oneECG printing and DigiFlexo technology, is the perfect solution for flexo converters wanting to produce short to medium run flexible packaging and shrink sleeves; a segment that is not profitably using digital technology. All presses demonstrated live were operating with direct integration to BOBST Connect, the advanced digital platform that offers next-level automation, digitalisation, and connectivity to support sustainable, efficient, and profitable production.
Closing the loop with connected workflows
As a central data centre, BOBST Connect seamlessly integrates every aspect of the workflow, from application management and pre-press setup to printing, converting, and quality control, collecting the production data. The ability to capture these valuable insights allows converters to enhance their business planning and optimise the entire production process. The platform is continually evolving with more functionalities added, such as the new BOBST-certified substrate library, job quality reports, and ‘Job and Recipe Management’, which deliver significant cost and waste savings by streamlining machine integration and enabling faster setup.
“BOBST has brought into reality the idea of the closed-loop workflow, from PDF to twin-PDF concept, addressing the main industry trends with easy-to-use machines, all orchestrated by BOBST Connect,” comments Cardinotti. “Our main focus is to provide customers with complete workflows that help them overcome a multitude of market challenges, allowing them to deliver consistent and high-quality results much quicker and with low waste, without having to rely on highly skilled operators.”
Colour consistency across technologies and applications
Another crucial issue addressed at the event was how to maintain colour consistency across different types of technologies, applications, and over time. Beyond labels, converters are also leveraging BOBST inline flexo technology to produce a range of short-run flexible packaging applications, such as pouches, shrink sleeves, and flow wraps. With such a highly complex market, it is a great challenge for converters to maintain the consistency of brand colours from job to job.
During the event, BOBST, together with its network of partners, demonstrated how oneECG guarantees cross-compatibility for production floor optimisation by digitalising colour management. By standardising the colours on press and automating the colour matching process – moving it from the pressroom into pre-press – machine operator skills will impact the outcome much less.
The benefits of oneECG printing on inline flexo presses also include savings on ink and plate costs, substrate waste reduction, faster setup, and a reduction in cleaning time and related consumables. Crucially, it allows shorter job runs to be printed more profitably, meaning converters can expand into flexible packaging, as demonstrated at the event with the MASTER M6.
ONE partner offering across all technologies and processes, from printing to converting
Guests could also experience the benefits of one global and extensive worldwide service organisation dedicated to support them with a wide range of services enhancing productivity and overall machine efficiency, from connected services (remote support) for fast resolution of problems to production ramp up support on-site.
Adding value through industry partnerships
BOBST is not operating alone in shaping the future of packaging production but rather is collaborating with key suppliers to bring maximum value to customers. The event reinforced BOBST’s ecosystem of industry partnerships with the presence of Avery Dennison, DuPont, Esko, Lohmann, Kongsberg PCS, KURZ, and Sun Chemical.
“The new labels and flexible packaging competence center provides the ideal scenario for printers and brand owners to fully understand BOBST’s vision for the future of packaging production. Guests at the grand opening experienced our comprehensive portfolio of printing solutions in action and saw how our innovations and partnerships are shaping developments, while discovering how to boost and simplify their label production,” concludes Cardinotti.