Re-skilling Plate Management with Digital Technology
Nick Coombes speaks with Lars Lehner about FlexoMatrix, his company’s solution to automating a key process in the production chain that brings greater efficiency to flexo printing
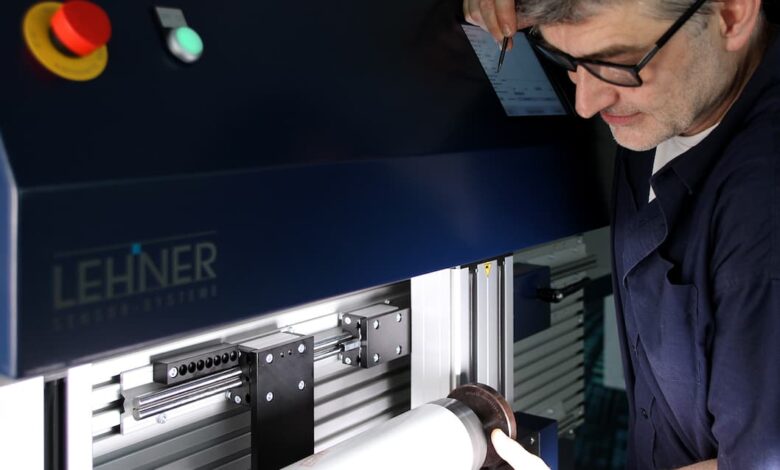
NC: What was the starting point for developing FlexoMatrix technology?
LL: It’s well known that skill levels have declined across the industry in recent years, while at the same time price pressure and short runs have continued to increase with more competition – so there was clearly a need to bring additional automation and greater accuracy to the print production process, and one area that had been largely ignored was that of plate mounting and management. The need was to link optimised data management to the production process with a practical tool that was easy to use and completely reliable. That’s why we developed a new technology platform – and we have called it FlexoMatrix.
NC: How does it work and what are the benefits?
LL: FlexoMatrix is basically a smart technology platform that automates plate mounting and offers job management support to the operator. It’s designed so that even lower skilled operators can assemble printing plates reliably, consistently and with the greatest accuracy. Its 360-degree print register capability offers very quick set-up times in the print room, which in today’s market of fixed colour palettes and short run work, is an important cost saving.
NC: Does FlexoMatrix have universal application?
LL: In terms of flexibility, yes, it does! A quick-change adapter system allows it to work with sleeves and all the popular types of cylinder so it’s a complete tool for all types of flexo pre-press from corrugated to carton and flexible packaging and labels. It handles all types of popular brands of flexo plates, including Asahi and Kodak as well as cylinder sleeves.
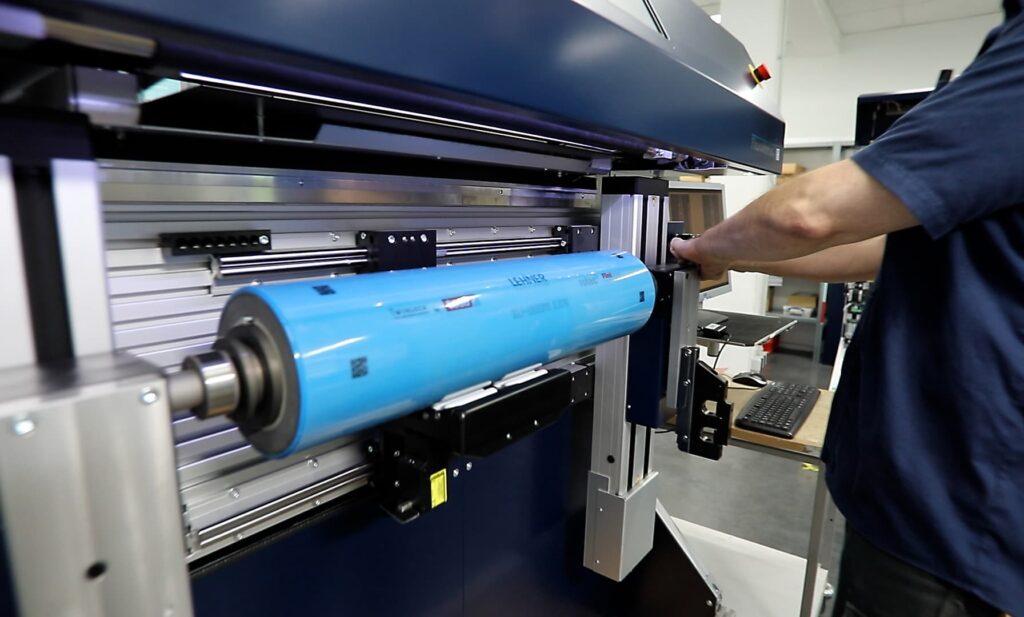
NC: How does it manage production data?
LL: It acts as a digital bridge between existing job management, pre-press, and the press room. By advanced consultation with the customer, we can adapt FlexoMatrix interfacing to fit the established job management system, which saves time by avoiding the laborious manual input of job data like print length, cylinder type, direction of travel, offset, and so on.
NC: Is this just a speed-up process?
LL: No, it also adds a layer of product security because each printing plate is identified before it’s mounted, and its print direction is checked. This makes plate mixing and the subsequent problem it causes a thing of the past. It also brings a new level of transparency to work planning, which allows production to be optimised. This means shift patterns can be planned better and the reasons for time and cost overruns are more easily identified and localised.
NC: How does the FlexoMatrix system approach plate identification?
LL: It’s based on smart disk identification that makes for easy and accurate archiving of used plates. Where, for example, an operator may have struggled to read the text written on plates and therefore been unsure how and where to file them, the FlexoMatrix system of ‘plate ident’ makes this an automatic process and removes another variable in the production chain.
NC: How does this help?
LL: Because FlexoMatrix knows which plate is mounted onto which sleeve or cylinder, it reduces the risk of error by providing a new degree of traceability. Information on plate ‘mileage’ and location can be obtained with additional scanning technology on the press and in the plate archive.
NC: What else does it offer?
LL: It feeds the existing job management system with extra useful information like the plate and cylinder number, the accuracy of the mounting process, the print direction in which the plate was mounted, and a time and date line. This gives a whole new level of data for more efficient planning and job handling. The result is greater process efficiency and lower cost, and therefore improved margins.
NC: How would you sum up the benefits to a company considering investing in FlexoMatrix?
LL: The improvements come is several layers. First, there is improved 360-degree register quality and register transparency across all the flexo printing presses in the plant. This makes for a significant reduction in waste material with every job change and allows more jobs to run on each printing press. Then, the recorded results set a new benchmark for subsequent and repeat print jobs, which allows the company to optimise its production efficiency. Well-known issues relating to register become a thing of the past and printers gain standardisation and operator independence. For these companies, FlexoMatrix offers an easy and important step into the future of flexo print production.
NC: Do the benefits vary depending on company size?
LL: Yes, they do, because each company is unique and has its own issues and priorities. For the larger print houses, FlexoMatrix acts as a comprehensive and reliable technology platform that utilises their existing job data management to automate and provide transparency in their print workflow. Smaller companies like it because it helps them to optimise their existing processes and allows them to focus on producing more volume of high-quality print from every flexo press. Large company or small, I’d say they all benefit from the added operator independence and FlexoMatrix’s unique 360-degree controlled mounting process that translates into the highest accuracy on the market. It’s ‘win-win’, whichever way you look at it!
NC: Aside from FlexoMatrix, what else does your company offer?
LL: We have a wealth of experience in automated print workflow and have established a worldwide reputation for partnering companies in their drive for improving production efficiency with automation. By pushing data-transfer and adding smart automated components wherever they are applicable, we can demonstrate reduced set-up times and lower material waste with every job change. Reports from our users vary, but real-life improvements of between 10% and 50% are common.
Dr Lars Lehner is Managing Director of Lehner GmbH Sensor-Systeme
107 Comments