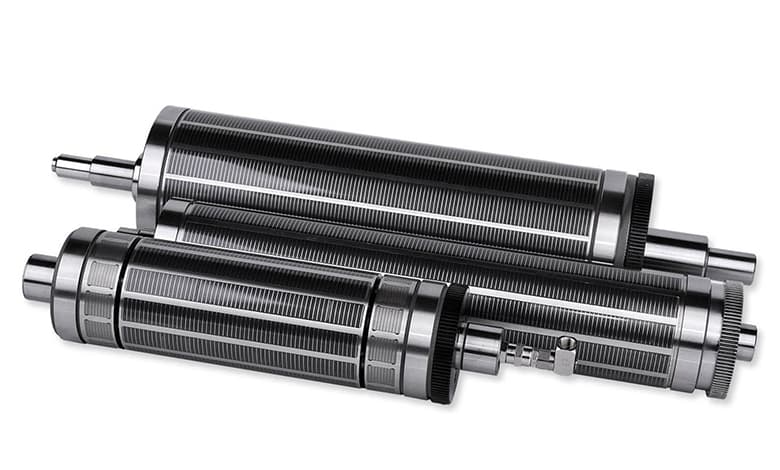
Minimizing Variables in the Die-Cutting Process
The die-cutting process demands precise control to achieve consistent results. Cutting dies must be carefully machined and sharpened to tight tolerances to ensure they only penetrate specific material layers. Male and female embossing dies must align perfectly to produce the desired embossed or debossed textures. Similarly, foiling dies require precise structures to ensure clean foil separation.
To maintain consistent quality, label and packaging tooling must adhere to strict tolerances. However, variables such as setup, pressure, distortion, materials, and temperature can impact outcomes. Minimizing these variables is critical to achieving precision and reliability in the process.
The Role of Cylinders, Anvils, and Rollers
In label printing and converting, various cylinders, anvils, rollers, and related components like bearers, gears, and shafts play a significant role in performance. These tools are used in flexographic, lithographic, gravure, and rotary printing systems. Key components include print sleeves, anilox rollers, rotary cutting cylinders, magnetic cylinders, anvil cylinders, and support rollers.
Before diving into specific types, understanding their components and positions is essential:
- Bearers: Smooth edges that enable rotary movement and absorb impression pressure.
- Shafts: Fixed or removable components that connect cylinders.
- Gears: Maintain accurate registration by meshing precisely with adjacent gears.
Regular maintenance, lubrication, and monitoring of wear ensure the longevity and functionality of these components.
Cylinder and Roller Manufacturing
Cylinders are primarily machined from aluminum or steel using CNC milling machines. These machines operate with high precision, capable of achieving tolerances within 0.0001 inches (0.00254 mm). Multi-axis CNC machines can execute complex milling operations, including embossing patterns and cylindrical grinding. Final finishes may involve polishing or protective coatings to improve durability and performance.
Printing Cylinders and Sleeves
- Printing Cylinders: These form the foundation of label printing systems and must ensure accurate contact with inking rollers or substrates. Plate cylinders, blanket cylinders, and impression cylinders are critical for lithographic, flexographic, and letterpress processes. Surface treatments like anodizing protect cylinders from scratches during plate mounting.
- Printing Sleeves: Lightweight sleeves simplify handling, reduce setup time, and eliminate gear marks often caused by wear in conventional cylinders. Synthetic sleeves are cost-effective but may degrade over time. Aluminum sleeves, though slightly heavier, retain precision and durability, making them a long-term investment.
Anvil Cylinders
Anvil cylinders, typically made from hardened steel, provide support during die-cutting by enabling smooth rotation and precision cutting. They are commonly positioned below the die but can adapt to specific configurations. Options include:
- Straight Anvils: Standard for routine operations.
- Stepped Anvils: Compensate for different liner materials or worn dies, extending tool life.
Manufacturing involves processes like vacuum hardening, gear cutting, grinding, and polishing to ensure exceptional hardness and accuracy.
Support Rollers
Support rollers are placed beneath anvil cylinders to balance pressure and tool weight. They prevent deflection during high-pressure operations, ensuring consistent cutting and reducing tool strain.
Magnetic Cylinders
Magnetic cylinders are designed for use with flexible dies, offering cost-effective alternatives to conventional rotary dies. Made from high-tensile tool steel and fitted with permanent magnets, they provide exceptional precision. Magnetic cylinders enhance cutting accuracy and extend tool life, especially when paired with thin PET liners requiring ultra-tight tolerances.
Maintenance options include magnet repair, bearing replacement, and regrinding to restore specifications.
Anilox Rollers and Sleeves
Anilox rollers regulate ink transfer in flexographic printing by delivering controlled ink volumes to printing plates. Key features include:
- Cell Patterns: Laser-engraved cells determine ink volume and distribution.
- Materials: Options include chrome-plated copper or ceramic-coated steel.
- Sleeves: Anilox sleeves offer lightweight handling, easier registration, and reduced shipping costs, making them ideal for modern gearless presses.
Precise specifications such as line screen count, cell depth, and depth-to-opening ratio ensure optimal ink delivery. Anilox tools must align with print requirements for halftones, spot colors, or solids.