Mimaki Eyes Textile Industry with New DTF Printer
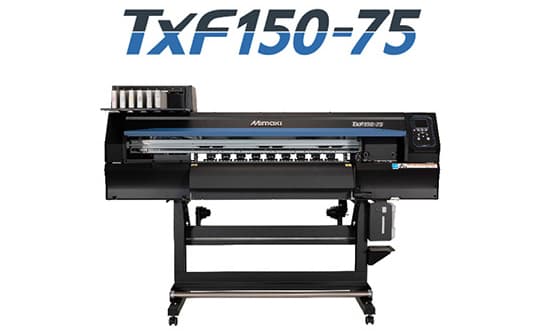
Global industry leader and manufacturer of wide-format inkjet printers, cutting plotters, and 3D printers Mimaki has announced the launch of TxF150-75, its first direct-to-film (DTF) printer and PHT50 heat transfer pigment ink for DTF. Sales of Mimaki’s DTF printing products, which include printers, inks, and RIP software, targeting apparel and textile printing applications, will begin in April 2023.
DTF printing is extensively used in the textile and apparel industry, particularly in T-shirt printing in the wearable printing market. DTF is a printing method where the design is printed directly on a special transfer film which is then sprinkled with hot-melt powder and is then heated and dried to form a transferable ink layer on the film. This ink layer is then transferred on a fabric, such as a T-shirt, by a heat press to complete the finished product.
TxF150-75 has a maximum print width of 800mm, and uses a piezo printhead with a print resolution up to 1440dpi. The PHT50 ink coming in five-colours (CMYK + white) is scheduled to gain the ECO PASSPORT certification by the end of March, a requirement to obtaining OEKO-TEX international safety standards that guarantee the safety of textile products, reduces environmental impact, and is also friendly to the customers’ work environment.
To overcome ink ejection defects, Mimaki has adopted a degassing ink design that uses aluminum packs as the printer’s ink packaging form. In addition, the Mimaki Circulation Technology (MCT) function effectively suppresses pigment precipitation by periodically circulating white ink to prevent problems such as white ink clogging, thereby improving print stability. The printer is also fitted with Mimaki’s proven Nozzle Check Unit (NCU) and Nozzle Recovery System (NRS) that automatically detects missing nozzles to minimize downtime and enable seamless printing.
Currently, silk screen printing which is widely used in the wearable printing market requires the preparation of plates, making it unsuitable for small-lot production. Moreover, full-colour printing requires time and labour to make plates for each colour. The heat transfer method using rubber sheets, though commonly used, requires manual weeding, a process involving manual removal of unwanted portions of the transfer when fixing the printed design on the fabric.
In recent years, direct-to-garment (DTG) printing has become a popular method, which uses inkjet printers to print designs directly on the garments and fabrics. Though DTG printing does not require plates and is a good choice when it comes to complex images or images with many colours, it does require fabric preprocessing and manual handling by the operator at each step in the printing process.
Comparatively, DTF printing eliminates plate preparation and weeding used in conventional printing, and since it enables unattended printing process operation, DTF is rapidly being adopted as a cost-effective and labour-saving technology.