Saudi Paper Inks Deal with Toscotec for Sixth Production Line
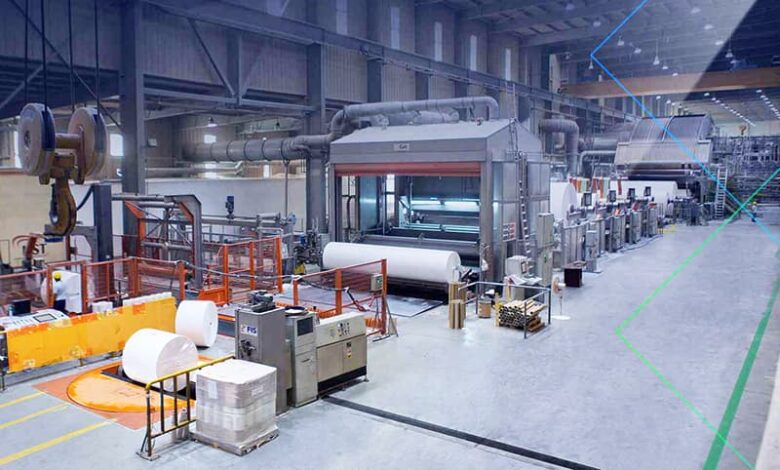
Saudi Paper Manufacturing Company (SPMC) has signed a non-binding agreement with the Italian company Toscotek, a leading edge technology and customized solutions provider to paper producers around the world, to purchase a production line for sanitary paper rolls estimated to cost 300 million Saudi riyals (around $80 million).
SPCM said in a statement that the agreement relates to supplying a new machine as the sixth production line with a design capacity of 60,000 tonnes per annum, increasing the company’s total annual production capacity of raw tissue paper rolls from 1,90,000 to 2,50,000 tonnes. The new line is based on the company’s expansion strategy to increase market share and support national exports to countries in the Middle East, Africa, and Europe, in line with the kingdom’s Vision 2030.
The Dammam-based tissue-paper manufacturer also said that the deal will be financed through the company’s operating revenue, and the rest through local banks and financial institutions.