IML: Transforming Packaging with Advanced Technology
How In-Mold Labeling Enhances Product Appeal and Sustainability
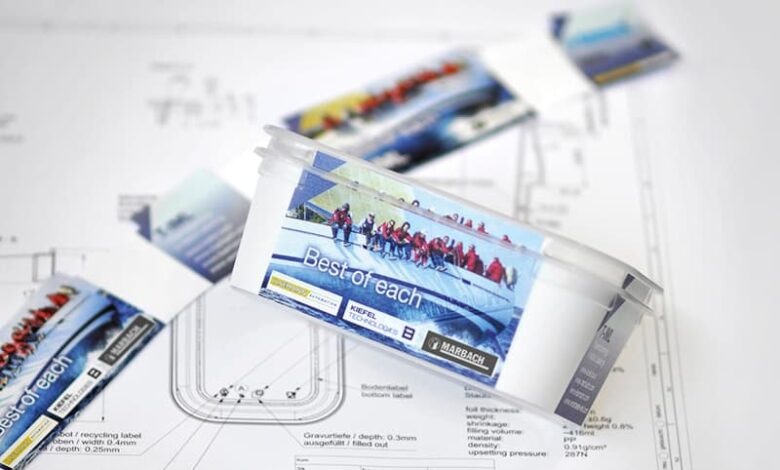
In-mold labeling (IML) is a process where a pre-printed decorative film is inserted into a mold prior to the formation of the plastic container. During this process, heated plastic pellets or resin are introduced into the mold. As the plastic takes shape within the mold, it seamlessly fuses with the label, forming a unified product.
In-mold labels undergo surface printing and are then coated with an over-lacquer or topcoat, utilizing either roll or sheet printing methods. The adhesive component of these labels is integrated into the film either through coextrusion, extrusion coating, or as a separate coating applied at various stages of the printing process. Once printed, the labels are precisely die-cut to the required size and shape, and then assembled in stacks for use in the in-mold labeling process.
The Evolution of In-Mold Labeling
Originating in Europe during the 1970s for injection molding and later in the United States for blow molding, in-mold labeling (IML) has revolutionized the process of decorating plastic containers. This technique involves placing a pre-printed label within the mold before the plastic is injected, blown, or thermoformed, resulting in a seamless and integrated label on the finished product.
In-Depth Look at the IML Process
Blow Molding: In this IML process, a label is placed in an open mold, held in position by vacuum ports or electrostatic attraction. The mold then closes, and molten plastic resin is extruded into it, conforming to the shape of the object. The label merges with the hot plastic, becoming an integral part of the container. This method is predominantly used for bottles and hollow containers.
Thermoforming: Thermoforming IML differs slightly. Here, the label is placed in the mold, and a sheet of plastic is laid over it. The heated mold then closes, shaping the container and integrating the label into it. This process is widely used for the manufacturing and decoration of container lids.
Injection Molding: In injection molding IML, the label is inserted into the mold, and heated plastic is injected, forming the container around the label. The plastic granules are fed into a screw tool, melted, and then injected into the mold. This method is commonly used for solid containers and offers high precision in label placement.
Substrates Used in IML
The substrates for IML have evolved from paper labels to more advanced filmic materials compatible with the primary container material, enhancing recyclability. These substrates are designed with properties like good lay-flat characteristics, a range of finishes (matte, gloss, metallics), and resistance to issues like curling and scratching.
Advantages and Disadvantages of IML
IML’s advantages include enhanced label durability, integration with the container for increased strength, resistance to harsh conditions, and simplified filling and packaging operations. However, it faces challenges like inflexibility in rapid decoration changes, high initial equipment costs, and extended production times.
Comparison to Wet Glue Labels
While IML offers a more durable and integrated labeling solution compared to wet glue labels, the latter still holds advantages in terms of cost-effectiveness, flexibility for design changes, and lower initial investment.
Specialized Applications and the ‘No Label’ Look
In specific applications like yogurt packaging, IML has been innovatively employed using form-fill-seal machines. These machines allow for the labeling of containers in aseptic conditions, enabling lighter container walls and efficient production. Additionally, IML technology has made the ‘no label’ look increasingly popular. This involves the use of transparent film labels that give products a sleek, label-free appearance while still providing necessary branding and information. This aesthetic, combined with the durability and recyclability of IML, offers brands a unique way to stand out on shelves and appeal to environmentally conscious consumers.
Sustainability and Recyclability in IML
A significant benefit of IML is its contribution to sustainability and recyclability. Since the label and container materials are similar, typically both being polypropylene or polyethylene, the entire package becomes fully recyclable. This uniformity in materials simplifies the recycling process, as there is no need to separate the label from the container. It aligns with the growing global demand for sustainable packaging solutions, reducing the environmental impact while maintaining high-quality aesthetics and functionality.
IML stands as a pivotal innovation in packaging, offering a blend of durability, aesthetics, and environmental sustainability. Its continued evolution and adaptation to various molding techniques, including the sophisticated ‘no label’ look, underscore its significant role in the future of packaging technology.