HEIDELBERG’s 10 Innovations Eases Costs, Skills Shortage
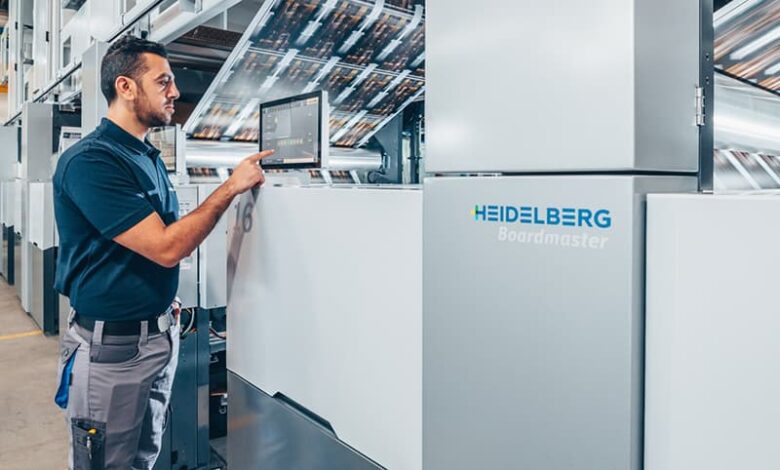
The printing industry faces two main challenges – continuing cost pressure and a progressive shortage of skilled workers. Industry giant Heidelberger Druckmaschinen AG (HEIDELBERG) offers print shop solutions that can help with both these key issues.
“Cutting-edge sheetfed offset technology from HEIDELBERG is becoming ever more productive compared to the previous models. In certain cases, it can even double a print shop’s output thanks to the combination of Push to Stop and Performance Services. By automating the printing process, we are also helping to compensate for the difficulty in filling posts,” says Dr. David Schmedding, the company’s Global Head of Sales & Marketing. “At the same time, sheetfed offset remains many customers’ method of choice for cost-effective high-volume printing,” he adds.
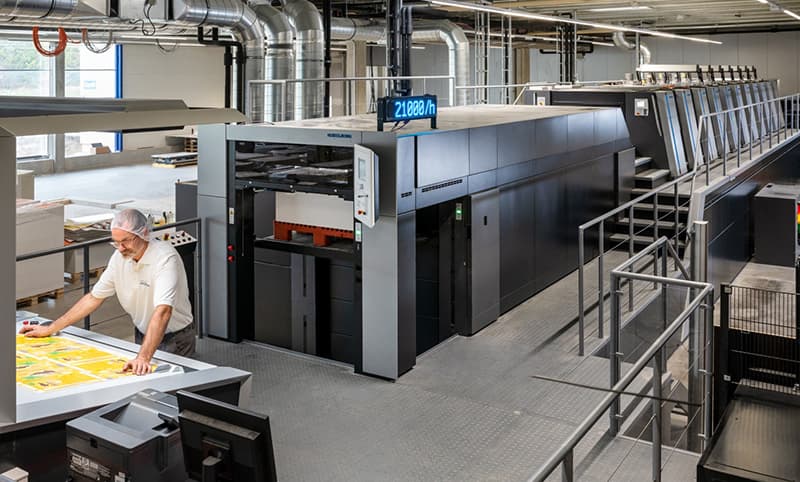
Ten selected innovations:
Exceptional efficiency: With a printing speed of 21,000 sheets per hour, HEIDELBERG’s Speedmaster XL 106 makes it possible to increase net output in folding carton production by up to 10% compared to the standard configuration with an output of 18,000 sheets per hour. For in-mold label production on the Speedmaster XL 106, HEIDELBERG offers a performance package designed for the specific requirements of in-mold materials that enables up to 15% higher production speeds to be achieved.
HEIDELBERG also offers a highlight that is not based on offset technology for high-volume folding carton printing. The company’s new Boardmaster flexographic web printing system is all about efficiency, achieving double the productivity of comparable systems in folding carton production. The Boardmaster boasts an availability of up to 90% and a maximum printing speed of 600 metres per minute, which is equivalent to around 38,000 sheets per hour in A6 format.
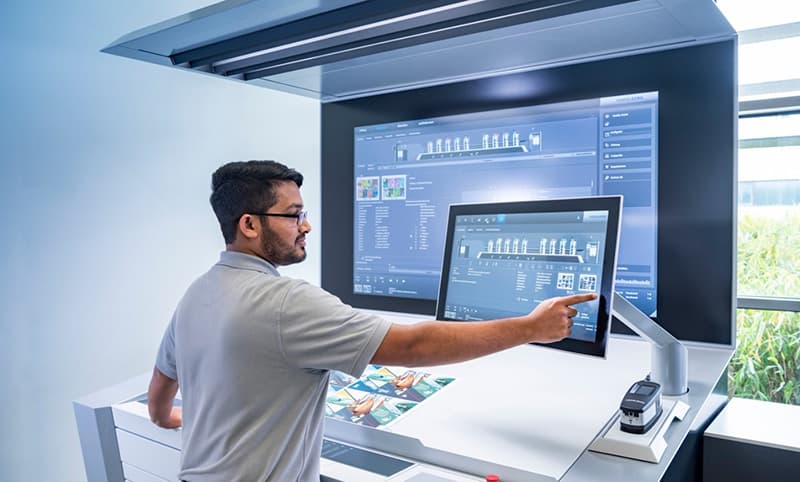
Automation to mitigate skills shortage: As it moves toward an autonomous pressroom, HEIDELBERG is equipping its Speedmaster presses with ever more fully automated processes that relieve the strain on operators. Prinect software seamlessly integrates all the steps involved in print production into consistent processes – from incoming orders through to shipping – into an end-to-end workflow, while the established Push to Stop concept ensures highly automated operations that can also be linked to third-party workflows. As a result, print shops are seeing a significant easing of their staff’s workload.
Besides boosting productivity, Plate to Unit – HEIDELBERG’s award-winning fully automatic printing plate logistics solution – can also mitigate the shortage of skills at print shops. By almost fully automating the process of supplying and removing printing plates on the press, this solution ensures reliably high productivity and reduces the risk of plates being damaged. This system is a real game-changer when it comes to fully automatic plate changing.
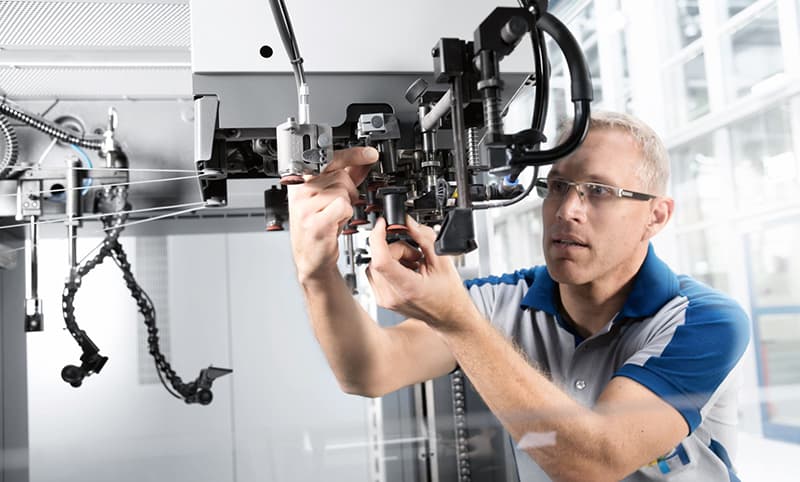
Intelligent algorithms: The use of artificial intelligence (AI) makes life easier for print shops by supporting the automatic configuration of complex production parameters. Initial functions implemented by HEIDELBERG include the process optimization solution Preset 2.0, the intelligent assistance systems Intellistart 3, Wash Assistant, Powder Assistant, and Color Assistant Pro, and the company’s Performance Advisor Technology (PAT). PAT acts as a kind of digital colleague. It visualizes and structures data, also offering practical suggestions and tips for improvements that boost productivity and save on resources.
Sustainability cuts costs: The energy efficiency of printing presses is improving all the time. HEIDELBERG is working on as many different parameters as possible on its systems to achieve this. Enhanced standby functions, ultra-efficient blowers such as those in AirStar Pro air supply cabinets, and a workflow, for instance, that minimizes waste all lower costs. The company’s special consulting teams visit customers and hold energy workshops to analyze where they can save on resources and cut costs.
Lots of individual targeted measures all add up and have a big impact. The latest Speedmaster XL 106-6+L consumes some 40% leass energy per thousand sheets than an equivalent Speedmaster CD 102-6+L from 1990. This is achieved thanks to numerous functions that either reduce waste (such as Analyze Point for waste reporting and Prinect Inpress Control) or save on material (such as Powder Assistant and FilterStar).
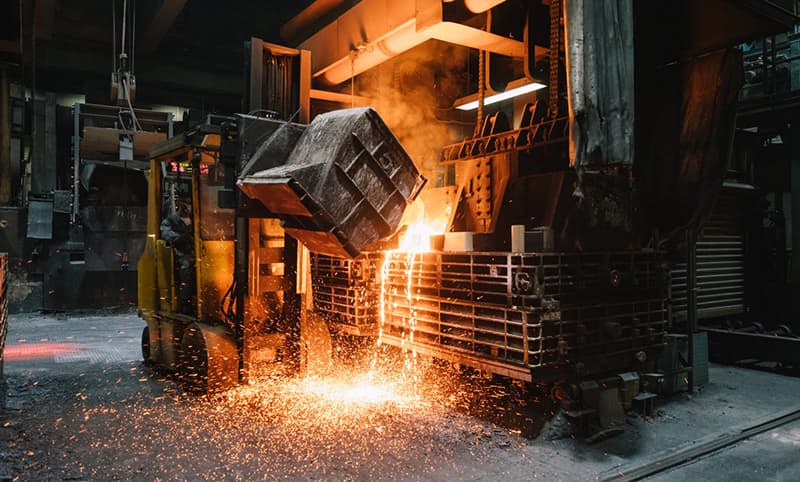
Digital press setup via touch control: One HEIDELBERG solution can boost print shop performance in just a few clicks. The Speedmaster Operating System with intuitive operator guidance based on touch control – HEIDELBERG User Experience (UX) – ensures user-friendly control of the press. The Speedmaster Operating System is controlled via a 24-inch multi-touchscreen. Operators can call up settings with a click, while the scalable operation can be flexibly adapted based on the requirements profile (Smart Setup). What’s more, the system offers innovative gesture control and integrated help functions in 27 languages.
Results make all the difference: End customers see and feel the difference. Accurate colour reproduction plays a key role in the modern brand world of print shop customers. Colours must match perfectly, and it is especially important for premium products to also feel premium to the touch. HEIDELBERG’s highly automated colour and quality measurement systems ensure absolute repeat accuracy and colour fidelity in commercial and packaging printing. This, too, can be achieved on a highly automated basis.
The unique Prinect Inpress Control 3 spectral measurement system finds the print control strips, paper white, and register marks fully automatically, and starts ink control without any intervention from the operator.
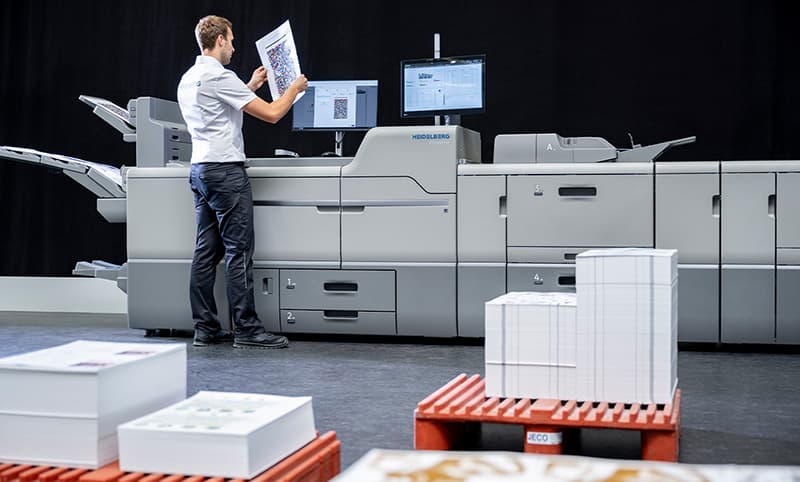
Two printing technologies in one: HEIDELBERG seamlessly combines digital and sheetfed offset printing. The new digital printing systems Versafire LV and Versafire LP are equipped with an enhanced Prinect Digital Frontend (DFE). In conjunction with a new user interface, this software ensures a flexible, standardized, highly productive, and intuitive combination of offset and digital printing technology.
Precision, down to the last detail: To provide its customers with presses that operate smoothly for long periods, HEIDELBERG has always focused on precision. This is already evident from its production of core components. The HEIDELBERG foundry at Amstetten, considered one of the most modern in Europe, manufactures high-precision components for the company’s presses and also for industrial customers in a variety of sectors. Over 3,000 components including machine guards, cylinders, gears, and many others are developed and manufactured at the site.
Global service network: HEIDELBERG boasts of a comprehensive sales and service network worldwide with over 2,000 employees at 250 sites in 170 different countries. The company’s services also extend to scalable contract models and remote maintenance operations that help reduce downtime and safeguard customers’ investments. In addition to this, the HEIDELBERG service portfolio helps print shops cushion the effects of the skills shortage by training staff and optimizing processes. Consulting and training for both management staff and employees focus on equipment-related process optimization at print shops.
“Pay-per-use” model: HEIDELBERG provides everything a print shop needs for stable and effective production, and does so from a single source. Besides service, consumables, software, training, and consulting, the Subscription Plus Model the company offers in collaboration with insurance company Munich Re also covers the press itself. The amount customers pay for the all-in package depends on their output, that is to say the number of printed sheets they produce. Since Subscription Plus also includes the press, customers do not need to invest in this. Instead, they pay to use the press, also based on a price per sheet (capex to opex).