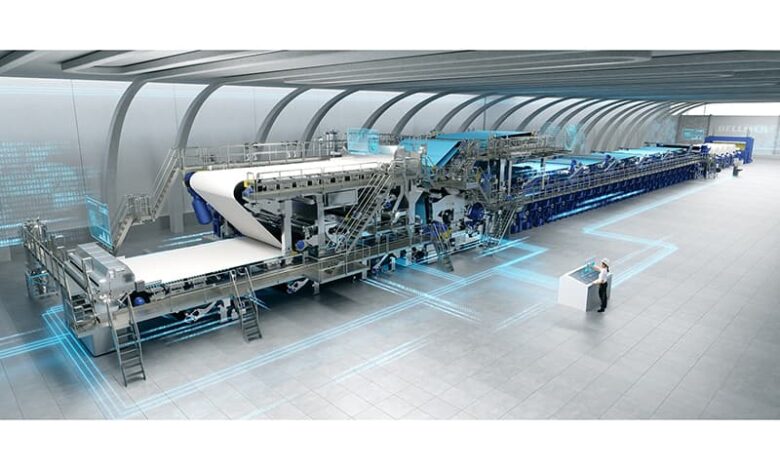
In the “Circular Competence” interview series, the VDMA Printing and Paper Technology Association asks its member companies about their plans, solutions and challenges on the road to a circular economy. What can the industry do to minimise the ecological footprint of packaging and other printed products?
With his brothers Martin and Philipp, Erich Kollmar keeps the family-run Bellmer Group on a growth course. Its success is based on sophisticated plant technology for resource-efficient paper and pulp production, for effective water treatment and for closed-loop processes.
Do you use recycling and waste avoidance concepts in your own production?
Of course. For us as a company with a very high level of vertical integration, disposal costs alone require us to separate all residual materials by type and to return them to material cycles wherever possible. Resource protection and cost reduction go hand in hand in this area. For about a decade now, we have also been reducing the variety of materials we use, for example stainless steel, in order to streamline our processes. Of course, this also makes it easier to separate by type.
What Circular Economy solutions do you offer your customers?
Our plant technology enables water cycles in many industries. The most important market is components and complete solutions for solid-liquid separation in the production of paper, cardboard, packaging, special and security papers, or fibreboard. Here it is also a question of optimising the processes for increasing recyclate proportions. In addition, we are successful with our solutions in around 60 other industries and fields of application. Be it waste water treatment on cruise liners and merchant ships, temporary water treatment in Olympic villages or the removal of stone polish from the process water in gravestone production. In addition to new plants, we also offer our customers conversions and refurbishments of their plants. In close cooperation with our customers, our teams check which components actually need to be replaced and which have not yet reached the end of their life cycle. The latter will, of course, continue to be used. In such projects, we also learn how to optimise the design of new parts so that they are easier to recycle – or even better – can be repaired with little effort instead of having to be replaced. In this way, we gradually create guidelines for design and material selection that bring us closer to the circular economy. Some of these are small changes: In combination with the right material, decentralised permanent lubrication bushings save a lot of lubricant instead of centralised lubrication. And where components turned or milled from the solid in special machine construction are redesigned in such a way that they no longer have to be completely replaced in the event of damage, but the replacement of an adapter is sufficient, this also contributes to energy and resource efficiency. Our engineering teams have explicit backing for such optimisations. Bellmer has had a master plan for continuous improvement for many years. We take a look at our solutions at regular intervals and discuss what we can improve about them. Sustainability and environmental aspects play an important role in this.
How does this affect your research and development and the cooperation with customers and their material suppliers?
Exciting new partnerships are emerging. One example is the cooperation with a Dutch manufacturer of boards that are pressed from recyclates in paper production without the addition of glue. His goal is to use this process to produce durable advertising displays as well as pressboard for the furniture industry or trade fair construction. Thanks to the absence of glue, these can be recycled again and again. The first plant is already running at full capacity. The company is currently building a second one, to which we are contributing our separation technology. Material cycles and resource efficiency have long been a topic in our research and development. We consider the entire system and work continuously to reduce the number of components and materials used. Here, too, ecological, and economic considerations are directly intertwined.
Is the demand for your Circular Competence increasing worldwide – or is this more of a regional phenomenon?
Many clients are more receptive to environmental arguments and are serious about sustainability. But by no means all of them make total cost of ownership considerations before making investment decisions. Often it is only about the purchase price, not about the energy and resource requirements or how long a machine will last. The more developed the markets, the more customers are willing to accept additional costs for more efficient solutions. But even in highly developed markets we notice that some players are more concerned with appearances than with reality. Greenwashing is and remains an issue. But overall, the willingness to invest in clean technologies is growing.
Environmental protection is often driven by regulation. Are the framework conditions right for entering the Circular Economy?
I think that narrowing the focus to CO2 falls short in many cases. Because it then depends too much on where the system boundaries are drawn whether a product is considered environmentally friendly or not. If we run electric vehicles on coal-fired electricity, nothing is gained. And if the steel is not produced domestically but imported, German CO2 emissions will drop. But for the global balance it is more important how modern a steelworks is and which energy sources it uses. So, we have to look at the system as a whole instead of setting arbitrary system boundaries to ease our consciences. But this becomes too complex on a global scale – and the higher the complexity, the more loopholes open up for those who are more interested in quick profit than in sustainable solutions. There is a need for measurable, comprehensible, and globally applicable parameters whose compliance is monitored. It would be conceivable to assign an ecological footprint to a metre of welding seam or a kilowatt of engine power that is oriented towards the most efficient process on the market – and that cannot be compensated for in any other way. This is the only way to ensure that climate- and environmentally friendly solutions quickly find their way into the markets. On the other hand, unilaterally imposed complicated regulations create unfortunate distortions of the situation. In competition, they precisely weaken those who spend a lot of time, energy, and money on the development of clean technologies.