Automation Shaping the Future of Packaging
A Transformative Force Revitalizing Packaging Manufacturing
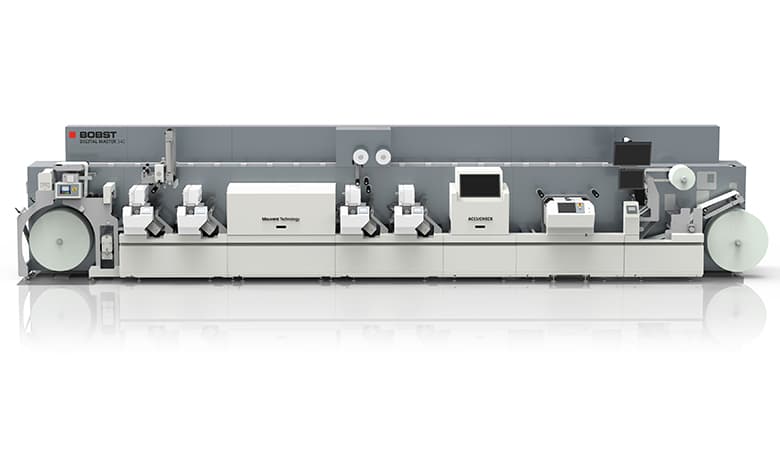
drupa 2024 featured two key ‘megatrends’ – the first being sustainability, and the second digitalization. Nobody in the industry denies these are indeed the big topics of the current era, but there are others that are equally defining the future of packaging – namely automation, and with it, connectivity.
Indeed, when BOBST set out its industry vision to shape the future of the packaging world several years ago, the four stated pillars were automation, connectivity, digitalization and sustainability. These four, interconnected pillars have completely transformed the industry in the last few years. But it was noticeable at BOBST’s stand during drupa 2024 just how far automated solutions have come – and the impact they are having for converters and other players in the industry.
It was striking that Jean-Pascal Bobst announced at drupa that BOBST “will become a software company.” That is because data is becoming so integral to our industry. In the future, everything will be driven by data, and using data requires software.
And it is data that drives effective automation.
Automation requires that machine and process data be captured, analyzed, and used for optimization in real-time across fully digitized processes. Therefore, the existing digital gaps in today’s processes need to be gradually closed. BOBST has developed its cloud-based digital platform, BOBST Connect, to meet these requirements. All machines connected to it can transfer their production data to the cloud and receive data from it – from the setup process through adjustments during ongoing production to quality reporting during and at the end of the production. The era of isolated machines in packaging manufacturing is over.
So how is automation enhancing packaging manufacturing at every step?
- Shifting machine settings to prepress
Tasks previously performed at the machines can now be moved to the prepress stage, particularly the setup processes. An example is recipe management for quality control with ACCUCHECK. A single click is all it takes to transfer the recipes to the ACCUCHECK systems, which then configure themselves automatically.
This brings several advantages: the setup process is accelerated, the work of machine operators is significantly simplified, and input errors are eliminated.
Label manufacturers using BOBST’s digital printing machines are already familiar with the convenience of automatic machine settings. They simply need to import their customers’ PDF files into BOBST’s Digital Front End, define the setup data for the machines, and send the jobs to them. Immediately afterwards, the printing machines start running. This is how BOBST machines will generally operate in the future.
One of the most exciting announcements at drupa 2024 was the new DIGITAL MASTER 55 all-in-one platform, which is specifically tailored for folding carton production. This platform, which features full inline and automated printing adjustment capabilities and quality inspection, is ideal for runs up to 6,000 B1 equivalent sheets where it can significantly reduce production time by up to 80% and reduce costs on short runs by as much as 80%, while eliminating waste, logistics, and downtime required for traditional production processes. It is equipped with a Digital Front End that allows customers to deliver small runs of folding cartons on the same day they are ordered.
- Integrating Tools
BOBST’s digitalization process does not stop at the machines. The tool management solution TooLink for the die-cutting process was another highlight at BOBST’s drupa booth. With TooLink, die-cutting tools are equipped with digital chips that store tool numbers. Once the tools are inserted into the die-cutters, the machines recognize the individual jobs based on the numbers and automatically make their basic settings. This automation step further reduces setup times in the die-cutting process and eliminates input errors.
In addition to job data, the production and performance data of the die-cutting tools are stored in BOBST Connect throughout their entire lifecycle and are available at the touch of a button. The complete inventory of die-cutting tools is possible in the cloud. Converters can see a comprehensive overview of their condition and can replace or repair worn tools in a timely manner.
- Machine automation solutions
At this year’s drupa, BOBST showcased many solutions for automating various work steps at the machine level. These included the groundbreaking Digital Inspection Table (DIT) for comprehensive quality control in packaging manufacturing. It enables proofing of a file using digital projections on printed products, allowing real-time visual representations to be aligned with digital proofs across all steps of the production process.
In labels, BOBST’s digital and all-in-one (AIO) presses are designed to deliver advanced automation, superior print quality, and seamless end-to-end processes. As an example, a converter could produce multilayer labels in a single pass instead of making multiple passages involving more than one operator. By integrating multiple processes into a single machine, our extremely modular all-in-one solutions significantly reduce the need for additional equipment and labor, leading to lower production costs.
Other examples of powerful automation solutions include the widely used smartGPS system for digital automation of the central cylinder flexographic printing setup process and the new smartGRAVURE system, which significantly simplifies and speeds up the setup process for gravure printing machines with digital automation technology. With onePRINT, this solution also includes a closed-loop system for automatic color corrections in the printing process.
In BOBST’s coating machines, the Strain Control Solution automatically controls web tension during production, while the Reflex Solution monitors and regulates coating weights. In vacuum metallizing, the new AI-based BOBST intelligent Metallizing Assistant supports machine operators by automating the metallization process, thereby increasing its performance while improving the stability of the product quality.
- Robotics
Integrating robotics into its portfolio has made BOBST the only supplier in the market to offer complete packaging line equipment solutions for the corrugated board industry.
Bobst Novara is the new range of robotic systems for loading high-performance machines in corrugated and folding carton manufacturing, as well as for palletizing finished products.
Automating these work steps with proprietary solutions had long been on BOBST’s agenda. The company can now offer complete solutions for automated packaging manufacturing from a single source.
Automatically bringing other benefits
Automation also benefits the sustainability of packaging production – and thus the environmental footprints of the manufactured packaging.
Among other things, waste is reduced in digitalized, automated, and networked processes. Additionally, accelerated production processes mean more packaging products can be produced in the same amount of time, distributing the energy used across more products. It is increasingly evident how mutually beneficial all the pillars of the BOBST Vision are: automation, connection, digitalization and sustainability.
What about the future? Artificial intelligence (AI) and machine learning are already being utilized by BOBST and will continue to lead to new and exciting solutions. The company is already pursuing exciting projects in partnership with customers and industry partners. The future’s bright. The future’s automated.