The Big Three Target Label Printing Industry

The infamous Covid 19 has imposed new norm on all industries including printing and changed many rules and standards, not to mention that it has massively altered our daily lives. While commercial printing has perhaps been more affected by pandemic, packaging and label industries have largely remained unscathed and thrive as well. Meanwhile following a big drop in sales of offset sheeted presses it seems that all big three, Heidelberg, Koenig and Bauer and manroland Sheetfed recovered the lost ground and increased their sales considerably.
In a press release manroland said order intake for new presses at manroland Sheetfed, reached a 10-year record high in June. In February this year the company cancelled short-time working and started ramping up production at its factory in Offenbach. Peter Conrady, Head of Global Sales at manroland Sheetfed says: “The reasons for the very strong order intake in June, and for the year to date, are two-fold: Since the beginning of 2021 we have been seeing an increasing number of projects for both 700 and 900 size presses, as printers around the world began to regain investment confidence post Covid.”
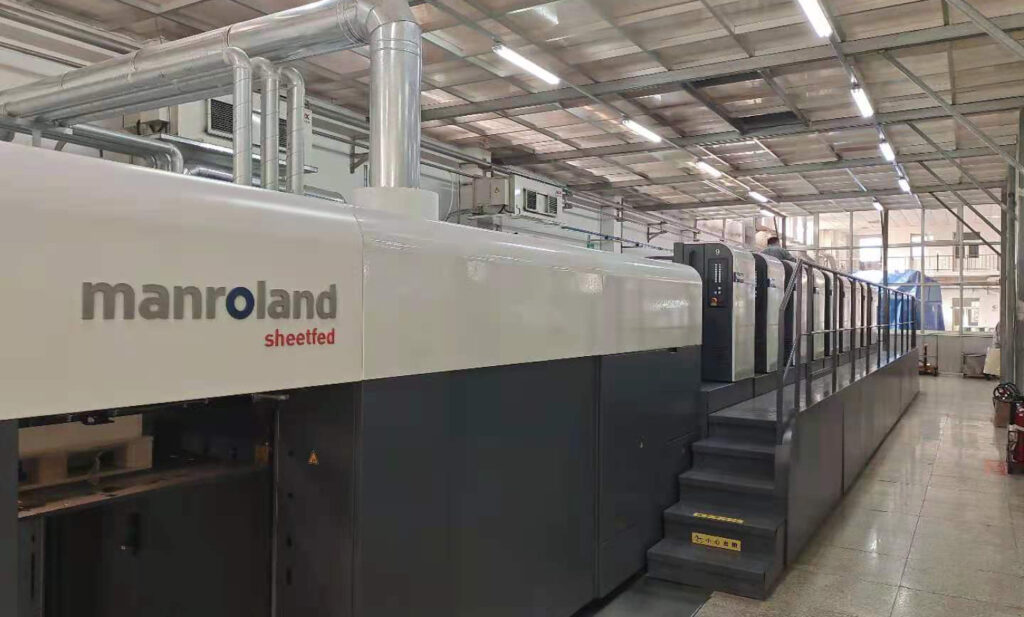
For their part Heidelberg and Koenig and Bauer also talk about increase in sales. However, the major order for the new sheetfed presses are coming mostly from package printers who are also involved in label printing including IML.
Printing IML label with sheetfed offset is nothing out of this world and printers around the world already are engaged with this lucrative market. However, there are some issues as well. First of all, feeding thin substrate into offset sheetfed press is problematic. Next challenge is drying of the ink specially for IML. In-Mould Labels (IML) print on synthetic plastic film (non-absorbent), so oil-based (oxidation) inks need time for air (oxygen) to dry. Tension control is another issue to deal with. The question is why bother? Why going through all these troubles to use offset for label printing? Narrow web press manufacturer are using offset printing units either in combination with flexo units or as a standalone machine, where almost all the units are offset. MPS which is one of the major manufacturers of narrow web press explains: “Offset is extremely good in CMYK and vignette printing. The technology gives outstanding results in the light and dark areas. Offset has low dot gains, like the new advanced flexo presses, but the size of the minimal dot in offset can be virtually zero. Offset is second best in solids; for that reason, 95 percent of all offset presses are combination machines with offset and flexo. Also, offset has relatively large setup wastes and times (it’s a more complicated process), and for that reason offset is used for relatively big order sizes.”
Sheetfed press manufacturers also want a piece of action
It seems that with highly automated new range of sheathed presses many previous technical issuesin relation with printing IML have largely been resolved.
Brand manufacturers increasingly demand all types of highly-creative and informative offset printed labels, so label printers are turning to sheathed press manufacturers for the fastest press speeds, excellent print quality, and proven substrate packages to deliver eye-catching, brand consistent labels for their customers.
“With the growing demand for labels, we’re accelerating our leading role in this very important market,” says Chris Travis, Koenig & Bauer director of technology. “This market is one of our main pillars along with commercial and packaging and we’re deeply committed to developing the latest innovations specifically for each market segment.”
While the U.S. demand for labels is forecast to rise 3.3% per year to $20.6 billion in 2025, Koenig & Bauer is seeing “significant growth”, especially here in North America as well as worldwide. What is drawing leading label printers to invest in Koenig & Bauer? Travis says that overwhelmingly it has been due to the firm’s superior technology that has convinced label printers to transition to Koenig & Bauer. “Our presses are producing labels at 20,000 sph unlike any other press on the market,” he says. “We have label customers breaking production records all of the time on our presses.”
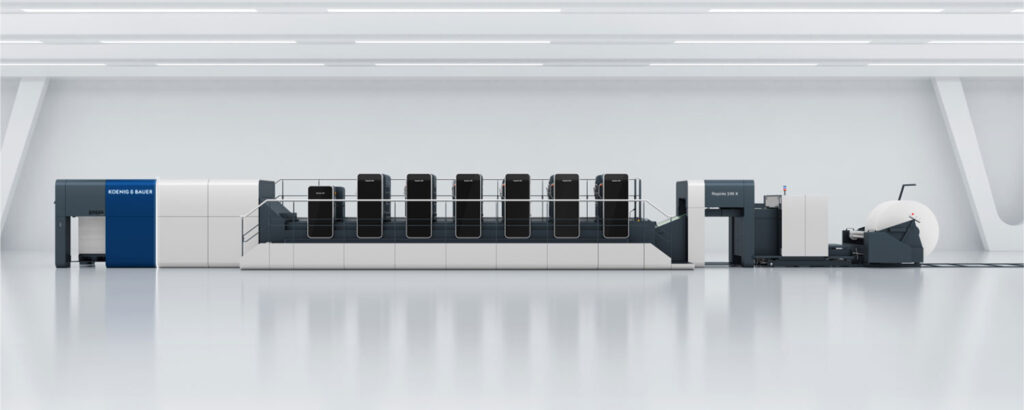
Koenig and Bauer claims what sets Koenig & Bauer apart is its unique complete process from substrate-in to label-out. This starts with the launch of the newly designed Rapida 106 X, a high speed 20,000 sph. On the other hand DriveTronic SIS, a unique side lay free system that allows for accurate registration of the thinnest substrates at max speed which is part of the important label sheet travel package, QualiTronic PDFCheck, an inline image inspection system that compares every printed sheet with the PDF data from prepress, and QualiTronic ColorControl, an inline color control system measuring every sheet, are extremely important for label production, in which each label must be consistent and include specific pertinent information.
The dynamic growth of in-mold labels is another important segment for Koenig & Bauer. “In-mold label printing is produced on thin plastic, down to 50 microns, and presents its own set of challenges. Due to our unique concept of sheet travel, from roll to sheet to delivery, which is unique to Koenig & Bauer, we’re able to efficiently and successfully print in-mold labels at the highest production speeds,” says Travis. “We’re also a leader in the LED-UV drying market, which significantly impacts the IML label market, if the label allows for energy curing. Since this type of label is printed on such thin substrates, it can be prone to distortion when subjected to the drying process. LED-UV emits no heat so it provides better control over the production process, allows improved registration, and provides higher quality while addressing the need for faster drying times and the ability to run a full pile in the delivery.”
Koenig & Bauer has placed so much emphasis on the label market that it has dedicated an individual area known as the Label Center in addition to its new Customer Experience Center in Germany. Visitors can witness the entire label production process on the new Rapida 106 X seven color with coater through to the new CutPRO X rotary die cutter. This new machine is equipped with the DriveTronic feeder, SIS (Sensoric Infeed System), label sheet guiding system, and AirTronic delivery and provides fast automation for job changeovers and an intuitive operating concept.
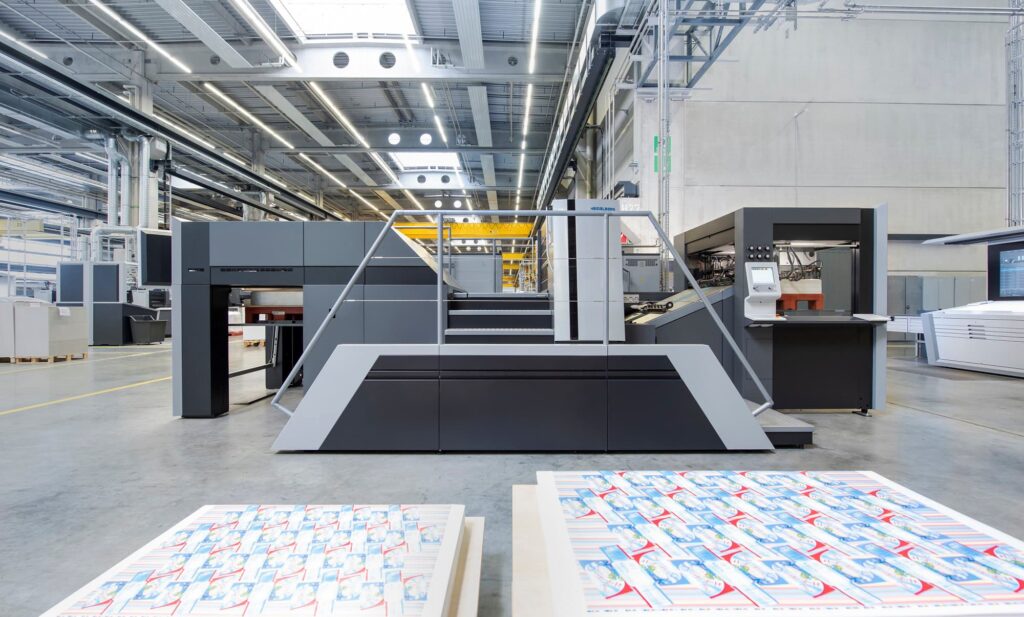
Heidelberg also eyes the lucrative in mold label market. According to the company the global label printing market to continue growing at an annual rate of around four percent. Growth is even expected to be above average in the in-mould label segment, which has not been affected by the COVID-19 pandemic. These labels are typically utilized in the food and cosmetics industries, and by companies producing chemicals for household and industrial use. The benefits of the in-mould process lie in its comparatively low manufacturing costs, good temperature and moisture resistance, and resource-friendly characteristics. For example, the polypropylene used for the labels and containers is 100 percent recyclable. Cutting-edge, increasingly efficient manufacturing processes are a further growth factor on the in-mould label market. Heidelberg’ new Speedmaster XL 106 with fully automatic presetting of all key print job parameters has gone through special modifications to the feeder and delivery, modified sheet transfer, and anti-static devices in order to make it possible to reliably process delicate plastic films just 50 microns thick at speeds of up to 14,000 sheets per hour. The high-performance model for conventional offset printing is equipped with three Y units (drying units) and a delivery with only one extension module. Even with extremely thin substrates, customers benefit from reliable sheet guidance and smooth travel through the press. The dryer modules are perfectly coordinated with the sheet travel and achieve outstanding drying results at maximum speeds. Distances for paper travel in the delivery remain short and, even at high speeds, sheets are completely stable when deposited on the delivery pile. The configuration with three Y units and highly efficient round-nozzle technology increases the drying capacity by 25 percent and also saves on energy costs, because the distance between the dryer modules and the substrate can be kept to a minimum.
The substrate is fed in roll to the machine and the redesigned CutStar generation 4 sheeter which is fully integrated into the Prinect workflow and the Intellistart system on the press for production based on the Push to Stop principle cut the roll into sheet and then sheets enter printing units. The Speedmaster XL 106- D I also equipped with jut just one die-cutting unit makes it easier for customers to move into IML production
Evolution Elite is The new generation of manroland sheetfed press. With its patented inking unit technology, the Elite can print with the high speed of 18,000 sph presses. InlineColorPilot 3.0, InlineInspector 3.0, new PressPilot, IntegrationPilot plus, plate changing systems and Autoprint are just some features. As an option, a new Evolution space-saving single drum perfector with speeds of 16,000 sph can be supplied as an option for commercial and packaging applications. With modification manroland pre I also more than able to print label.
So does sheetfed offset will shape the future of label industry? Perhaps not. but it will play a role and definitely make some inroad into traditional flexo market. The price is also another issue a complete set of modified sheetfed press with auxiliary equipment carry a hefty price tag. But sometimes in order to achieve the quality you are longing for you have to also pay its price.
One Comment