Transforming Challenges in Flexible Packaging into Opportunities
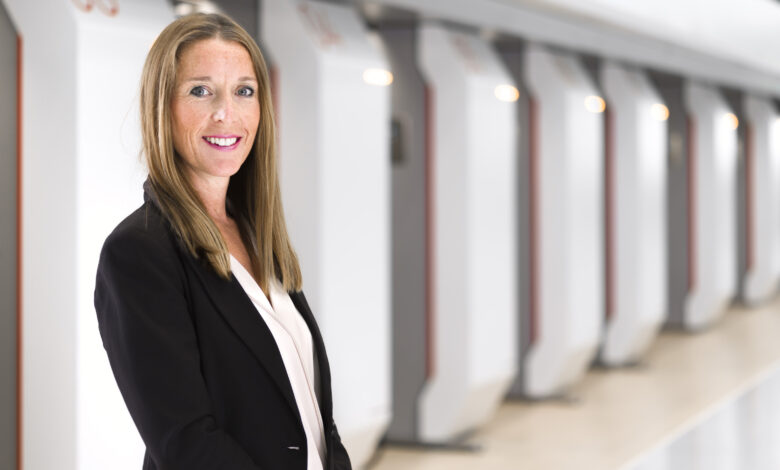
Building opportunities and a sustainable future in packaging industry
With a predicted annual growth rate in consumption of flexible packaging of 4.2%* to 40 million tonnes, which in value terms equates to 3.2% or $291 billion, during the period of 2021–2026,** there are many opportunities for converters to increase their share of, or expand into, this market. “However, the ‘journey’ over the next five years will be complex,” says Sara Alexander, Marketing and Communications, at Bobst Italia, “and we should not envisage traditional growth in volume or in value.”
There are many drivers that influence the future of flexible packaging (plastic, paper and foil), and these will have a direct impact on the evolution over the coming years. Thanks to its broad experience and end-to-end presence along the production workflow, along with partnerships with key industrial players and new substrate ready equipment, BOBST can help converters transform today’s challenges into opportunities and in the process build a sustainable future.
Sara continues, “We are witnessing an important transformation of the industry in terms of composition, as the type, structure, weight and cost of packaging is changing. To remain competitive and meet these new demands, converters need to embrace new capabilities to remain agile and more sustainable.”
Demands on the industry includes shorter time to market, which means the steps between file creation and the final packaging must be reduced; more agility in order to offer mass customization, variable data, and cost-effective production of short runs; quality control to ensure delivery of zero-fault packaging; and color consistency across multiple formats to satisfy brand owners worldwide.
Meeting sustainability challenges
Food packaging, which is the most resilient sector, represents around 75% of all flexible packaging demand. While consumers still expect packaging to protect its contents, they now also want it to be green and sustainable. The public perception of plastic packaging is extremely negative, fortified by influencers and climate change leaders.
Many leading brands, converters and packaging companies have made important commitments to make 100% of packaging reusable, recyclable or compostable by 2025. New materials that enable converters to meet these sustainability targets are being developed, but it is important to understand what impact these will have on the entire chain, from machinability and packaging quality to consumer habits.
In addition to these trends, the COVID-19 pandemic has increased awareness of product safety and hygiene making a lasting impact on the flexible packaging industry.
In order to take charge of the changes to the flexible packaging landscape, BOBST has positioned itself as a global solutions provider with a presence along the entire value chain. By moving away from being a traditional machinery manufacturer, BOBST is leading through innovation and shaping the future of packaging production, based on the four cornerstones – Digitalisation, Automation, Sustainability, and Connectivity – that together form the roadmap.
BOBST is present across all technologies, be it printing, die-cutting, laminating, metallizing, or coating, with strong know-how and experience, and we are strongly bonded with strategic partnerships throughout,” says Sara. “This puts BOBST in an extremely advantageous position, with knowledge at every possible phase with every possible technology. The benefit for our customers is that we can truly guide them through every stage from end to end.”
Sustainable materials from BOBST
Sustainability has moved from being a ‘nice-to-have’ to an essential requirement at all levels of production. BOBST is working intensively with many strategic partners along the entire value chain to create products and solutions to meet these sustainability requirements, with BOBST equipment.
“Today’s industry transformation is not about removing plastics, it is about creating new plastics, as plastics, when well produced, have a future,” states Sara.
BOBST’s first priority has been to develop sustainable materials, and that means finding mono materials, either PE-based or PP-based, that can be recycled but still maintain optimal barrier performance. The second priority has been to develop alternative fiber-based paper packaging solutions. These are naturally recyclable but pose a challenge in terms of their barrier performance. Thirdly, BOBST is active in the biopolymer space, developing compostable solutions that come to an end-of-life cycle.
In order to research, test, develop and prepare these sustainable, alternative flexible packaging solutions, BOBST is working with many high-level industry partners – from producers of film and raw materials, adhesives, lacquers, coating, and inks, to packing companies, brand owners and retailers.
With fully equipped laboratories and experts for guidance, BOBST Competence Centers are also fundamental to the research and development of these new substrates. By using these facilities, converters and brand owners can develop new solutions with fast time to market, minimum disruption for converters, maximum efficiency, and optimized costs.
Sustainability within the process
Developing water-based alternatives to solvents is another major priority for BOBST, and it is working on several projects to move this area of research forward.
A project with BASF had the objective to find a viable and approved water-based adhesive to replace solvents in lamination applications. The result was an approved market solution that leverages the power of the BOBST NOVA D 800 LAMINATOR.
Another success has been in the use of water-based inks for gravure printing, which until now has been limited. Bobst Changzhou, in China, has been amongst the first to develop successful water-based applications on its gravure presses, with its ink manufacturer partners. In December 2020, these efforts were awarded by the China Printing Industry Association.
However, sustainability is not only linked to the creation of new substrates or specific consumables.
BOBST oneECG printing technology is an example of sustainability within the process. By fixing the ink set, significant savings can be achieved, e.g., in gravure ink consumption, where leftovers and waste can be reduced by up to 50%. Other advantages include faster job changeovers and color matching, the possibility to run shorter jobs, and 100% repeatability of job quality and color consistency.
BOBST is working on many more projects that will secure the future of flexible packaging and tackle head on the challenges that the industry is currently facing. “It is important to understand that flexible packaging has a bright future,” concludes Sara, “but only if we embrace the opportunities and make new sustainable solutions possible.”
120 Comments