The Wide World of Narrow Web Presses
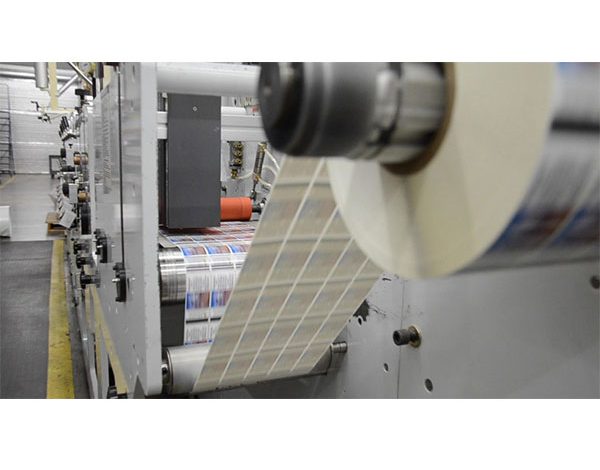
Exclusive Interview with Dieter Finna, founder of pack-consult.org
Narrow web presses are becoming more important in the world of label and package printing industry. Many commercial printers are also pondering to see if they can enter the lucrative label and flexible packaging market. In order to find out the advantages and the pitfalls of this technology that is growing in popularity and application we sat down with Dieter Finna, printing engineer with a broad expertise in the label printing and packaging industry.
The Term combination press or hybrid press has been introduced for some Time now, however are these two terms the same or they are different? What do manufacturers mean when they say hybrid press?
Combination or hybrid press are terms that are used more and more frequently in narrow web printing to describe the combination of different printing processes in one printing system. There is no standardized definition and every press manufacturer uses these terms to describe their own combination options. These can be purely conventional combinations of printing processes such as flexographic, gravure and offset printing with screen printing. Increasingly, however, the term hybrid printing press is used to describe the combination of conventional and digital printing in one machine system.
Using Servo drive motors has been a common practice for narrow web presses, some manufacturers are using several servo motors in each printing unit, some use master servo motor coupled with slave drives, so which one is better and why?
The equipment of a printing unit with several servomotors offers the possibility to control each cylinder individually. This brings various advantages with the different printing processes.
In flexographic printing, different peripheral speeds of the plate cylinder and anilox roller can be run and e.g. ghosting can be counteracted.
In offset printing, the press can achieve the necessary ink/water balance quickly by individually controlling the inking and dampening units at a higher speed compared to the web itself. The web only moves at a speed of 1 m/min, so that production quality is achieved with minimal start-up waste. The material savings over several years justify the higher costs for several servo motors in one printing unit.
Another argument in favour of separate servo motors is with press systems in which direct drive servo motors control the drive rollers. In this case a maximum reproducibility is achieved.
Commercial offset printers are facing an existential threat, especially after pandemic. Many of them are thinking entering label printing market and investing in narrow web press, what is your advice for them? Where they should begin?
For commercial offset printers the move to web-fed printing is certainly an opportunity if the entry into the packaging market is well considered. I see four important steps that should be done very carefully in preparation of the entry into the narrow web market.
- A proper market analysis to understand the market opportunities in different segments like self-adhesive labels, packaging applications (e.g. shrink sleeves, pouches) or special products such as tube laminates.
- Based on these findings a business case needs to be developed
- With this knowledge the right press can be selected to enter into conventional or digital narrow web printing.
At this stage, the timely adaptation of the entire workflow is also very important.
- The whole organization, especially the sales organization has to be trained on the new applications to serve the requirements of the new markets.
In many cases commercial printers need support from consultants or machine manufacturers during these steps, who can support them during their entry into a completely new market.
Narrow web Platforms have been evolved during last two decades, in your opinion what are the important changes that happened during development of narrow web presses and why?
There are many things that have changed so fundamentally in narrow web printing in recent years. One of the most important developments in narrow web presses is undoubtedly the automation of the machines and especially the automation for changing jobs. In many print shops, around two-thirds of their work consists of jobs with minor changes or repeats. For these jobs the complete make-ready data for the press is retrieved from a job file and all the necessary parameters such as web path, longitudinal and cross register, print parameters and the press’s die-cutting tool are set automatically.
Equally important is a new dimension in flexibility through the platform design of the printing presses. It allows the presses to be configured according to customer-specific requirements in general and for each print job individually.
A huge change in the print shops was achieved through digital workflows in connection with hybrid or digital printing systems, which resulted in highly efficient processes and significantly shorter throughput times.
It seems that there is a trend towards wider presses within narrow web press sector, because now converter want to print packaging with their narrow web press as well, do you think ultimately narrow web presses become mid web presses?
The last Labelexpo and developments after it show a clear trend towards wider presses in the narrow web area. However, that does not mean that the future will only be with wider printing presses. For label printing with its small runs, a narrow web machine with a width of around 300 mm width will also be sufficient in the future. Where both markets label and packaging printing are to be covered, wider machines offer the flexibility to react quickly to market opportunities, which, however, also creates higher investment costs in the machines.
Some Narrow web press manufacturer are now introducing multi substrate presses that can print on packaging films, self-adhesive labels, paper, even card boards, is this a right approach or is it preferable to configure narrow web press based on unique applications, for example only self-adhesive labels /or flexible packaging and so on.
In my view, this goes hand in hand with the question of wider machines. The quality of web transport determines how flexibly a press system can process different substrates. In today’s world, where market trends change quickly, the machine system should also be able to adapt very flexibly to market trends. This is especially important when we are talking about a product portfolio adjustment. If a machine can process a wide range of materials, this is the prerequisite for adapting quickly to new market situations without the need for investment in new machine systems or retrofitting.
What are the trends that will make narrow web printing Industry Thriving in the future?
In the near future we will see more technologies that allow automatic control of colour quality and consistency, use less ink and create less waste. Automation and digitalisation will advance. Conventional as well as digital printing systems operate on the basis of a networked automation workflow through machine-to-machine data exchange. Full automation of the printing process avoids machine stops and the operator’s hands and eyes are replaced by the accuracy of a digitised data matching system.
Especially in narrow-web printing we will see more and more hybrid printing systems where printing, embellishment and finishing take place in one operation. Automation makes it possible to control the previously complex work processes in such a way that they can be carried out inline with minimal waste and short make ready times. The digital printing systems allow a continuous industrial operation in 24/5 or 24/7 operation with a stability and productivity that have not previously been achieved.
The runs within label printing industry is becoming shorter while at same time brands are asking for more diverse printing, this means using digital printing to print label is gaining momentum do you think ultimately digital printing replaces flexo in future?
Digital printing shows an extremely impressive development and its potential is far from exhausted. Despite this fantastic development, it will still take many years to reach the standard of conventional printing processes in terms of the wide choice of substrates, the broad selection of ink systems and the requirements for migration behaviour. Digital printing, on the other hand, has the advantages mentioned in the question as well as the possibilities for individualizing each print, which again only digital printing offers. In my view, digital printing will complement conventional printing processes much more than it already does today. It will certainly be decades before it can cover all the requirements that are currently placed on conventional printing processes.
The level of automation in narrow web press is much higher now, some even claim a barber can learn to handle their machines after one-week training. Does this mean an end to operator skills for narrow web presses, or simply his or her role will change?
A more and more automated press environment means a fundamental change in the types of personnel and skills required throughout the printing workflow. With the data reported back to the operator by the printing press, which will still increase in the future, the task definition of an operator is also changing. Operators have an overall view of the entire process and no longer need to specialize in a repetitive manual or particular technical task. This does not mean, however, that the operator’s qualification in printing technology will be less. Even though many processes are automated and the operator receives suggestions from the press on how to eliminate certain deviations from standards, it is still the operator who decides and accepts or rejects these suggestions
And because the processes on a narrow web press are becoming increasingly complex and more and more printing and finishing technologies are coming together, the operator also needs this support in order to be able to produce the jobs efficiently. Printing press manufacturers offer trainings and support operators with a suite of applications in order to support them.
About Dieter Finna
Dieter Finna is a printing engineer with a broad expertise in the label printing and packaging industry. In his many years at Flint Group, he held various positions in the printing plate and ink business. He founded pack.consult in 2016, a platform for content marketing and packaging printing consulting.
3 Comments