Rapid Liquid Printing: Shaping Future of Industries
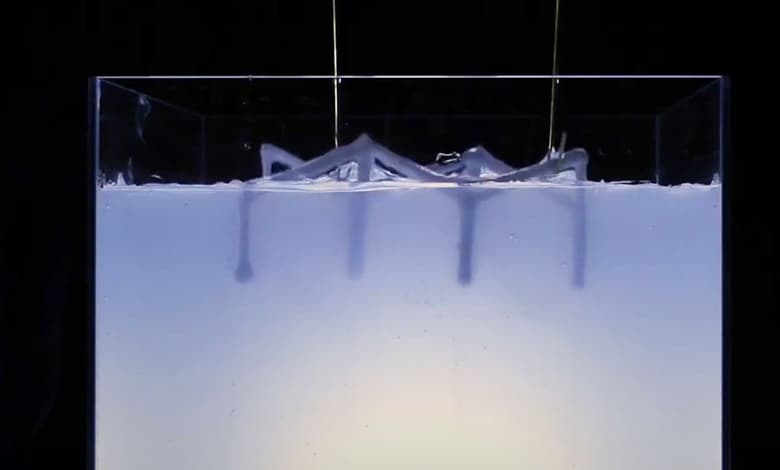
Futuristic technologies have left no industry untouched with radical changes, be it in workflow solutions or production. Printing and other related industries are also witnessing an unprecedented revolution, with 3D printing being one of them.
However, since its inception and despite the many advances, 3D printing technology remains in the realm of rapid prototyping, rarely being used for large-scale manufacturing. Currently, the greatest challenges for advancing 3D printing technology are small build volumes, long print times, high costs, and constraints on material versatility.
Rapid Liquid Printing: An MIT Spin-out
In 2018, the Massachusetts Institute of Technology (MIT) developed the rapid liquid printing (RLP) technology in the institute’s self-assembly lab to address current limitations of speed, scale, material qualities of 3D printers, and mass customisation through traditional manufacturing. The MIT spin-out is an experimental process that uses a tank of granular gel as a reusable support medium to greatly increase speed, size, and material properties in 3D printing.
All about Efficiency, Versatility & Speed
The RLP machine can freely print in any direction, rather than layer by layer on a flat surface, depositing liquid material into the granular gel to form 3D structures. The RLP deposition system can use any one- or two-part material that is photo or chemically cured, expanding the range of possible materials to include high-quality industrial grade rubbers, foams, and plastics, among others. It is platform-independent that can be implemented on any computer numerically controlled machine, robotic arm, or similar fabrication machine. Besides its ability to print on both small and large-scale objects, RLP is incredibly fast (up to 100-times faster than traditional or other 3D printing technologies), capable of printing a complex object within seconds. The technology frees designers from gravity, enabling production of even soft, stretchable, and durable products.
RLP in Fashion: Blending Tech & Creativity
The blend of this cutting-edge technology with creativity was introduced by Coperni, the Parisian ready-to-wear and accessories brand, in partnership with Disney. The most visually appealing example of this collaboration was Coperni’s swipe bag created using RLP technology that was showcased for the first-ever fashion show held at Disneyland Paris. The use of platinum-cured, recyclable silicone gives the swipe bag a liquid-like consistency, and exemplifies how fashion houses are pushing the boundaries of technology and sustainability in the industry.
The video posted by Coperni demonstrates the printing process. An aquarium of water-based gel holds the recyclable silicone’s printing process without falling apart. A very sharp, thin needle with a nozzle dives into the pool of gel and begins printing, churning out the silicone coloured in blue shade, and gradually shaping out to form the brand’s iconic swipe bag.
Shaping the Future
RLP is shaping the future of industries where industry-standard products are tailored to perfection in record time. The innovative process defies gravity and revolutionises non-planar printing. The groundbreaking approach enables the creation of complex designs that were previously impossible with traditional methods. RLP is an ideal platform for researchers, designers, and manufacturers.