Shortage of Key Raw Materials Impacts Costs
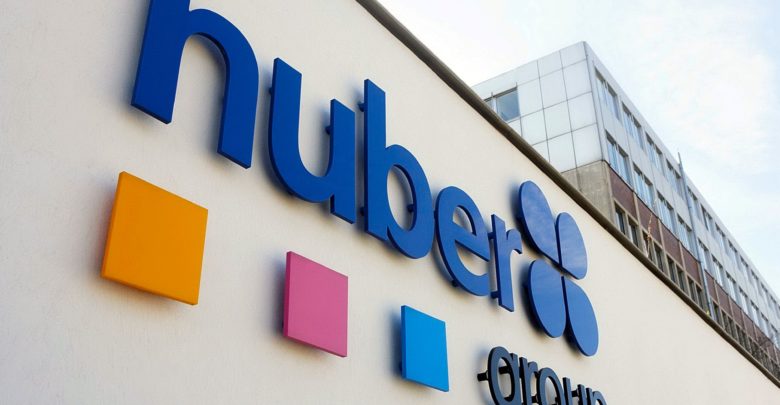
Printing ink manufacturer hubergroup states price increases for all energy curing inks and varnishes across Europe and the Americas with immediate effect. Depending on the individual product line, the raw material related price adjustments will range from 6 to 8 percent in specific areas.
“Due to severe shortage of key raw materials for these products which have a significant impact on our raw material costs, this price increase is inevitable”, says Carsten Zölzer, Director Product Management Sheetfed & UV within hubergroup.
Several challenges are now affecting raw material prices. In particular, photoinitiators, oligomers and monomers required for energy-curing printing inks are scarce on the market, which has a price driver effect. Reasons for this can be found in the closure of production sites of major raw material manufacturers in China, which are aimed at environmental protection, as well as the reclassification of certain photoinitiators, which have a significant impact on the market. Unexpected shortages due to force majeure add to this.
“While hubergroup is working intensively to cover the supply shortage and work on alternative solutions, this situation now reached a level, where we cannot mitigate cost increases in our product portfolio for energy curing products. Being a responsible, service- and quality-oriented supplier to the printing and packaging industry across Europe and America we will take up contact with our customer base accordingly about the product-specific increases that we need to apply,” said Carsten Zölzer.