Koenig and Bauer Launches New Metal Decorating Press
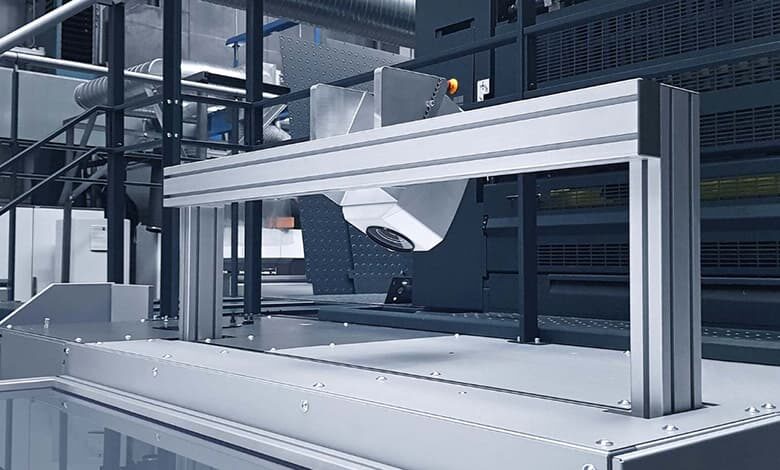
Seven years after the market launch of the MetalStar 3, of which over 400 printing units have been installed worldwide, Koenig & Bauer is presenting the new MetalStar 4.
The MetalStar 4 presents itself in a new design with innovative, pioneering technology. To meet the growing demands of the metal decorating market even better, the MetalStar 4 offers new functions and improvements in the feeder, state-of-the-art measuring technology and new functions for monitoring production and enhancing ergonomics. What remains unchanged is the proven MetalStar technology, such as the short and dynamic inking and dampening unit and high-precision register printing thanks to the sheet travel in the gripper closure, as well as the extensive automation features that reduce make-ready times to a minimum.
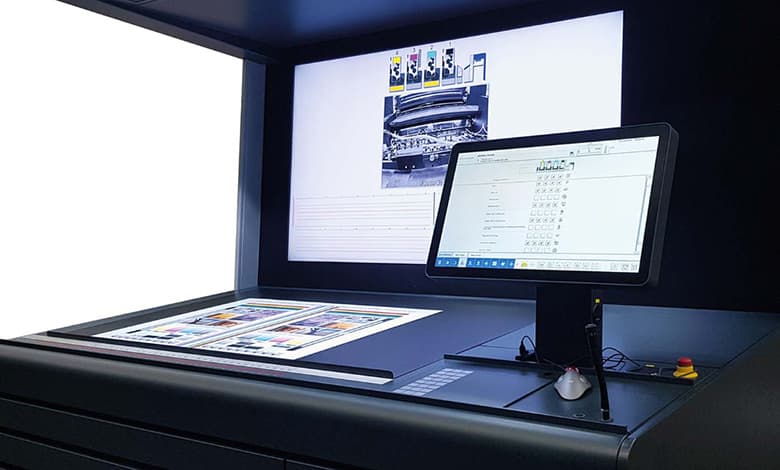
Some of the biggest innovations of the MetalStar 4 can be found at the feeder. Metal printing-specific updates such as new sensors, newly designed blow pipes and scrapers, and adjustments to the infeed table noticeably increase the reliability of the feeder. Even with challenging materials, the feeder’s reliability is convincing. The feeder is rounded off by a new touch panel on which the air setting can be made and stored for each job. For repeat jobs, the last setting can be conveniently loaded and production started directly.
The inline colour measurement and control system MetalControl, which is available for the MetalStar 4, measures the ink densities on each color patch in the print control strip or on individual colour patches and regulates the ink zones fully automatically every 10 sheets. This ensures that the specified target densities are always achieved and maintained within the print run. Independent of the operator or the time of day. In addition, MetalControl supports the operator in color setup for the print job. MetalControl can set up the target densities fully automatically in one print run, utilising a sandwich process. Alternatively, MetalControl can also be used to print individual print runs as usual during set-up. MetalControl then makes a setting suggestion after each print run.
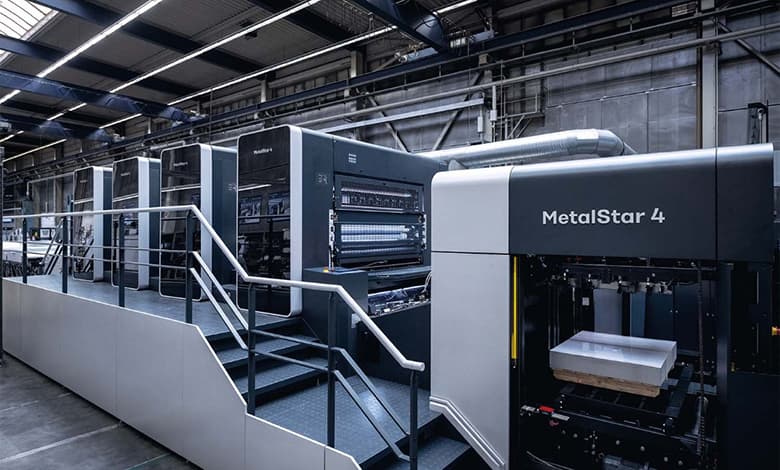
The new ErgoTronic console is the heart of the MetalStar 4. Thanks to the clear and modern software, the operation of the MetalStar 4 is intuitive. All settings are made via a 23″ touch screen. The console can be equipped with a 75″ wall screen on which the measuring results of MetalControl and the individual zone openings in each inking unit are displayed. In addition, a live image from one of the observation cameras mounted at neuralgic points on the line can be displayed here. This makes it easy to monitor critical positions live from the ErgoTronic console and intervene if necessary.
In terms of automation, the MetalStar 4 continues to lead the way in the metal decorating market. Features such as parallel washing of the blanket and impression cylinder with CleanTronic Synchro or parallel washing of the inking unit during blanket washing with DriveTronic SRW (Simultaneous Roller Washing) guarantee the shortest make-ready times in metal decorating. The fully automatic plate change FAPC (Fully Automatic Plate Change) is now even faster and has been equipped with a new infeed system that significantly enhances stability.
Each MetalStar 4 is customised directly to the individual needs of the customer and the application. From special equipment packages for UV and UV-LED printing, to a wide range of inline coating options, to the tried-and-tested sheet handling modules and Koenig & Bauer globally proven and highly regarded drying ovens.
87 Comments