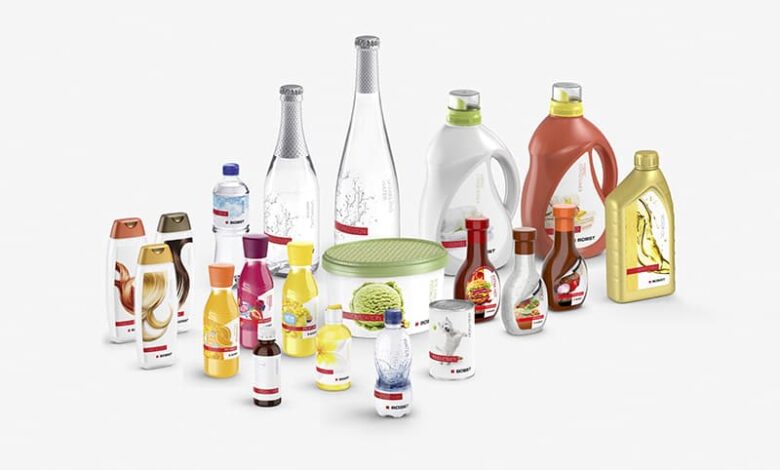
“As part of the oneLABEL portfolio which covers flexo, digital and All-in-One technologies, BOBST offers three inline press models for the label market that can be categorized as entry-level. The machines have been developed to make high-quality flexo production affordable for any printing company and to deliver fast ROI and sustainable operation at a low TCO.” Said Eric Pavone – Region Business Director Africa, Middle East and Turkey.
“The main type of customer that is looking for this type of flexo press include, in the more mature markets, micro and small companies that are focused on medium to long run production of pressure-sensitive labels; and in the emerging markets, converters that are either new to flexo printing or are upgrading from a different technology, in most cases letterpress.” Added Eric Pavone.
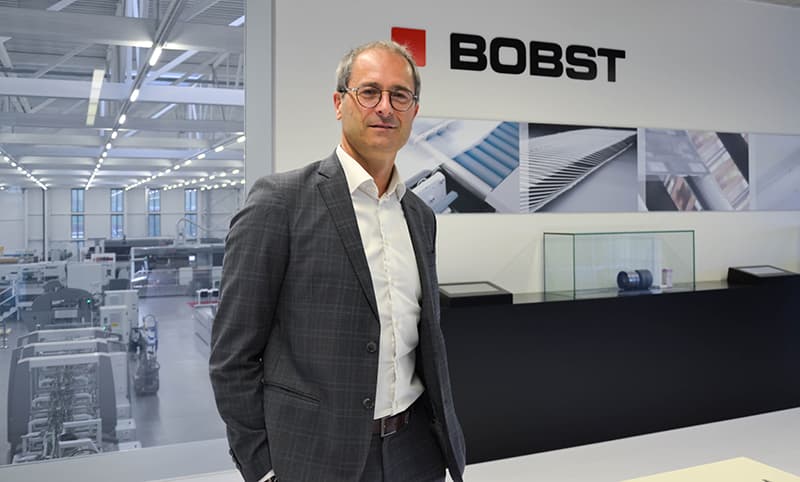
With relatively small profit margins in flexo printing, printers need to reduce waste, and be able to maintain productivity, consistency and quality day in day out. BOBST’s inline flexo presses are characterized by their robustness, stability and ease of operation, which ensures high uptime, repeatable quality and requires less operator skills to achieve an excellent outcome. Short setups and a high degree of automation further support printers to meet demands for fast turnaround and delivery of jobs, with a very competitive price to performance ratio.
The first press in the line-up is the BOBST NOVA M1, which can print on paper and self-adhesive label materials at 180 m/min. The fixed configuration has a width of 370 mm (14.5”) and eight print stations, a die-cutting unit and cold foil come as standard, with an optional delam-relam unit that can print in one color on the adhesive. Quick and easy to set up, it offers high uptime and fast time-to-market.
The BOBST VISION M1 is available in 370 and 430 mm (14.5 and 17”) widths in multiple configurations according to the requirements of the customer. It can print on a wide range of label substrates as well as light carton board extending the market opportunities. With up to 10 print stations and 2–3 die-cutting units, the VISION M1 can be set up to produce more complicated labels such as multi-layer peel-and-reseal coupon and booklet labels. The level of automation is also flexible with options to include Print Tutor cameras for fully automated register set-up and control, DigiGap automated die-cutting technology and Bambi advanced waste matrix rewinding for handling difficult label shapes.
“At a lower investment level, customers can choose to go for a set configuration, which is 370 mm wide version and has a smaller footprint. This is the VISION M1X, which has eight print units and one die-cutting station as standard but offers the same quality as the full version. It features Laser-Set pre-register system, Combo laminator and cold foil kit, and SnowBall waste stripping. It can be equipped with DigiFlexo technology for automated register set-up and control during production.
One of the BOBST innovations that all the presses benefit from is the specially designed Flower flexo heads, which enable much faster changeovers with less waste, than conventionally designed print units.” Concluded Eric Pavone.