Growing cost pressure and competitive pressure are forcing print shops to implement comprehensive process automation; packaging printer Kingraf in Brazil is the 2,500th user of a Prinect Production Manager; Prinect Touch Free continues to drive automation – workflow becomes a game changer
Automated production control in a hybrid workflow environment was the focus of the Prinect User Days 2025. More than 300 Prinect users, mostly from Europe, took part in the two-day event, which was held at the Heidelberg Congress Center and the ‘Home of Print’ at the Heidelberger Druckmaschinen AG (HEIDELBERG) headquarters in Wiesloch-Walldorf. The Prinect User Days is a welcome forum by users for users to exchange information about working with Prinect and the further development of this workflow technology.
Cost Pressure, Competitive Pressure Force Automation
HEIDELBERG launched the Prinect Production Manager at drupa 2016. The new subscription model replaced the previous license model. The Brazilian packaging print shop Kingraf, with over 300 employees, is now the 2,500th user of a Prinect Production Manager. “Our packaging processes require continuous innovation. Prinect is an indispensable tool for meeting our customers’ expectations,” says Kingraf CFO Claudia Markowicz Lopes, describing the importance of workflow technology.
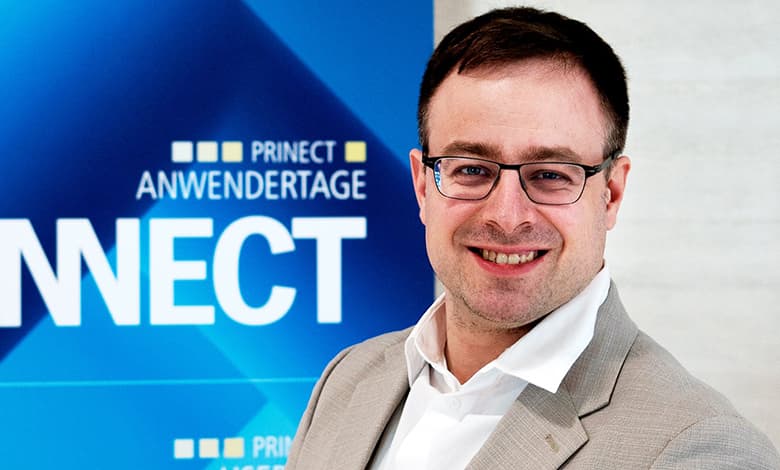
Galledia Print AG in Flawil, Switzerland, is one of those print shops that have also made great progress with process automation. The company has comprehensively automated the production of periodicals from the start of the job, through the allocation of pages in the intended imposition template, to digital job release via the Prinect Portal in the browser. Galledia currently controls the production of around 50 magazines via Prinect. “Prinect is the heart of our production and, in HEIDELBERG, we have a partner who brings the required expertise in the automation of production processes. It is a mutually beneficial development on an equal footing and, in the future, it will also extend to downstream process steps in the workflow through to the imaging of printing plates and beyond,” says Matteo Baschera, Technical Consultant at Galledia.
Trend toward Short and Very Short Runs Accelerate
It is the growing cost pressure and competitive pressure that are forcing print shops to optimise and automate their processes. Entrepreneurs and managers who do not transform their print shop in this direction even risk the existence of the business. Or, as Dominik Haacke, Chief Commercial Officer at mediaprint solutions GmbH, put it drastically in his keynote speech: “Print smart – or prepare to die.” Within three years, the Paderborn-based media service provider has transformed its production operations into the mediaprint smart factory, where print orders (B2B and B2B2C) are processed fully automatically via the Order Connect interface, from receipt of the order in a web store to delivery of the end product.
The switch from largely manual to automatically controlled processes is all the more urgent as the trend toward ever shorter print runs continues to grow. Printed matter is therefore increasingly being produced in a hybrid production environment in order to leverage efficiency and cost potential. While sheetfed offset is undisputedly the most economical process for longer runs, short and very short runs as well as jobs with individualised content are printed on digital printing systems, whether with toner or inkjet technology.
Meinders & Elstermann: Pilot Users of Data Capture App
HEIDELBERG customer Meinders & Elstermann GmbH & Co KG works in a hybrid production environment. The company uses offset and digital printing at its headquarters in Belm and four other locations. Meinders & Elstermann will also be the first company in Germany to use the Jetfire 50 industrial digital printing system. The processes are fully integrated into the digital workflow with the Prinect Business Manager management information system and the Prinect Production Manager. The data flows bidirectionally, i.e. the MIS sends the job data to production and in return receives the operating data from the individual cost centres. “We switched our production workflow to the Prinect system from HEIDELBERG in 2018. Thanks to the integration and automation, we were able to reduce the number of staff in prepress from twelve to seven,” says Marco Rassfeld. In addition to his duties as Head of Prepress and CtP, he is responsible for administration and support for Prinect workflow technology at Meinders & Elstermann.
As a pilot user, the company introduced the new Data Capture app last year. It is part of the HEIDELBERG customer portal and is used to capture and report back operating data from postpress systems. It will replace the previous Data Terminal. After the field test was launched in March 2024, Meinders & Elstermann connected the entire machine park with several folding machines, high-speed cutters, saddle stitchers, and a perfect binder to Data Capture by the end of October. The app uses browser technology and is independent of a specific operating system. “The app is self-explanatory and easy to use, so the training required was minimal,” says Rassfeld.
Prinect Touch Free Controls Production Fully Automatically
Conventional methods of managing print jobs and controlling their production are making it increasingly difficult to keep track of the sheer number of jobs, assign them to the appropriate output system in an orderly and logical sequence, and route them profitably through production. As Juergen Grimm, Head of Prinect at HEIDELBERG, said in his opening speech at the Prinect User Days 2025, “Print shops need to set the right priorities and focus on those jobs that promise growth. Prinect Touch Free and our approach to hybrid print production are becoming a game changer for economical and efficient production.”
In conjunction with the launch of the Jetfire 50, HEIDELBERG presented Prinect Touch Free at drupa 2024. The AI-supported cloud software puts high job volumes in short and long runs into a logical sequence. Resources are used optimally, resulting in efficient, cost-effective production. Prinect Touch Free calculates all possible layouts, plans the production sequence, and independently decides how a print product must be produced from the time an order is received to the end product – whether in sheetfed offset on a Speedmaster press, on a Jetfire 50, a Versafire, or on a digital printing system from a third-party manufacturer. In the decision-making process, Prinect Touch Free takes into account both the printing process and postpress right through to the end product.
For Rassfeld, HEIDELBERG is on the right track with Prinect Touch Free. “Prinect Touch Free will help us improve productivity significantly, make optimum use of our production technology, and increase volumes substantially, especially in digital printing with its many short runs.”